Heatsinks play a crucial role in managing the thermal performance of electronic devices, from consumer electronics to industrial machinery. The efficiency of a heatsink depends significantly on the material used in its construction, as each material offers different thermal conductivities, weights, costs, and other physical properties. This article provides a detailed exploration of the most popular materials used in heatsink manufacturing, examining their advantages, disadvantages, and applications. Additionally, it includes insights into how these materials impact the design considerations for effective thermal management solutions.
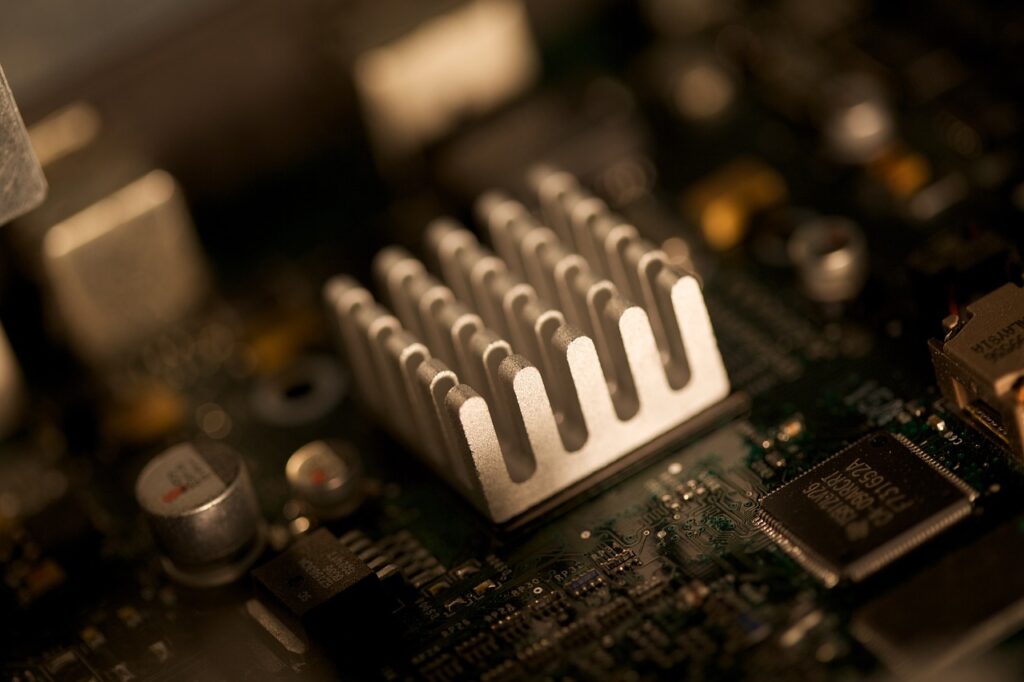
Aluminum
Pros:
- High Thermal Conductivity: Aluminum offers a good balance of thermal conductivity, typically around 235 W/mK, making it efficient for dissipating heat.
- Lightweight: Aluminum’s low density (about 2.7 g/cm³) makes it ideal for applications where weight is a concern.
- Cost-Effective: It is generally cheaper than other metals like copper, making it economically viable for large-scale production.
- Malleability: Aluminum is relatively easy to machine and form, which allows for complex shapes necessary for optimal heat sink designs.
Cons:
- Lower Conductivity than Copper: While effective, aluminum’s thermal conductivity is lower than that of copper, which can limit its performance in high-power applications.
- Corrosion: If not properly treated, aluminum can corrode, especially in harsh environments, affecting its thermal and mechanical properties.
Applications: Aluminum is widely used in consumer electronics, LED lighting, and PC cooling systems due to its cost-effectiveness and good thermal performance.
Copper
Pros:
- Superior Thermal Conductivity: Copper has a thermal conductivity of approximately 400 W/mK, which makes it excellent for high thermal conductivity applications.
- Ductility: It is highly ductile, which allows for creating very intricate and detailed heat sink designs.
- Resistant to Corrosion: Properly treated copper is highly resistant to corrosion, contributing to the durability of the heat sink.
Cons:
- Weight: Copper is significantly heavier than aluminum, which can be a disadvantage in portable devices where weight is a critical factor.
- Cost: It is more expensive than aluminum, which can be a limiting factor when cost is a concern.
- Difficult to Machine: Copper is harder to machine than aluminum, requiring more time and resources, which increases manufacturing costs.
Applications: Copper is often used in high-performance computing and servers, where maximum heat dissipation is needed and cost and weight are less of a concern.
Graphite
Pros:
- High Thermal Conductivity Along the Plane: Graphite can have thermal conductivities as high as 1500-2000 W/mK along the plane of the layers.
- Lightweight: It is lighter than metal-based heatsinks, beneficial for applications where weight is an issue.
- Flexibility: Graphite is available in flexible forms, allowing for use in applications where space is constrained or complex shapes are needed.
Cons:
- Anisotropy: Graphite’s thermal conductivity is highly directional; it conducts heat very well in two dimensions but poorly in the third, which can be a limitation depending on the application.
- Cost: High-quality graphite can be expensive and harder to source compared to metals like aluminum and copper.
Applications: Graphite is used in applications such as laptops, smartphones, and other space-constrained devices needing efficient heat spreading with minimal weight.
Silicon Carbide
Pros:
- High Thermal Conductivity: Silicon carbide offers thermal conductivities around 270 W/mK, suitable for various applications.
- High-Temperature Stability: It retains its strength and stiffness at high temperatures, unlike metals that can soften.
- Chemical Resistance: Silicon carbide is resistant to most acids and alkalis, enhancing its durability in harsh environments.
Cons:
- Brittleness: Silicon carbide is very hard but also brittle, which can limit its use in applications where mechanical stress is a factor.
- Cost: The material and processing costs of silicon carbide are relatively high compared to more common materials like aluminum.
Applications: Due to its high-temperature stability and good thermal conductivity, silicon carbide is often used in applications involving high temperatures, such as aerospace and automotive components.
Composite Materials
Pros:
- Customizable Properties: Composites can be engineered to have specific properties, combining materials to optimize conductivity, weight, and thermal expansion coefficients.
- Versatility: They can be used to achieve properties that are not possible with single-material solutions, such as improved thermal conductivity and reduced weight simultaneously.
Cons:
- Complex Manufacturing: Composite materials often require complex and precise manufacturing processes, increasing production costs.
- Inconsistencies: Variability in the manufacturing process can lead to inconsistencies in performance from one batch to another.
Applications: Composite materials are used in advanced electronics and military applications where specific thermal management properties are required that cannot be met with single-material solutions.
Conclusion
Choosing the right material for a heatsink involves considering the specific requirements of the application, including thermal performance, weight, cost, and environmental resistance. Aluminum and copper remain popular due to their balance of cost and performance, while materials like graphite and silicon carbide offer solutions for specialized applications. Composite materials represent an evolving area that promises customizable solutions for complex thermal management challenges.
This comprehensive guide aims to assist designers and engineers in selecting the most appropriate material for their heat dissipation needs, ensuring both efficiency and innovation in their thermal management solutions.