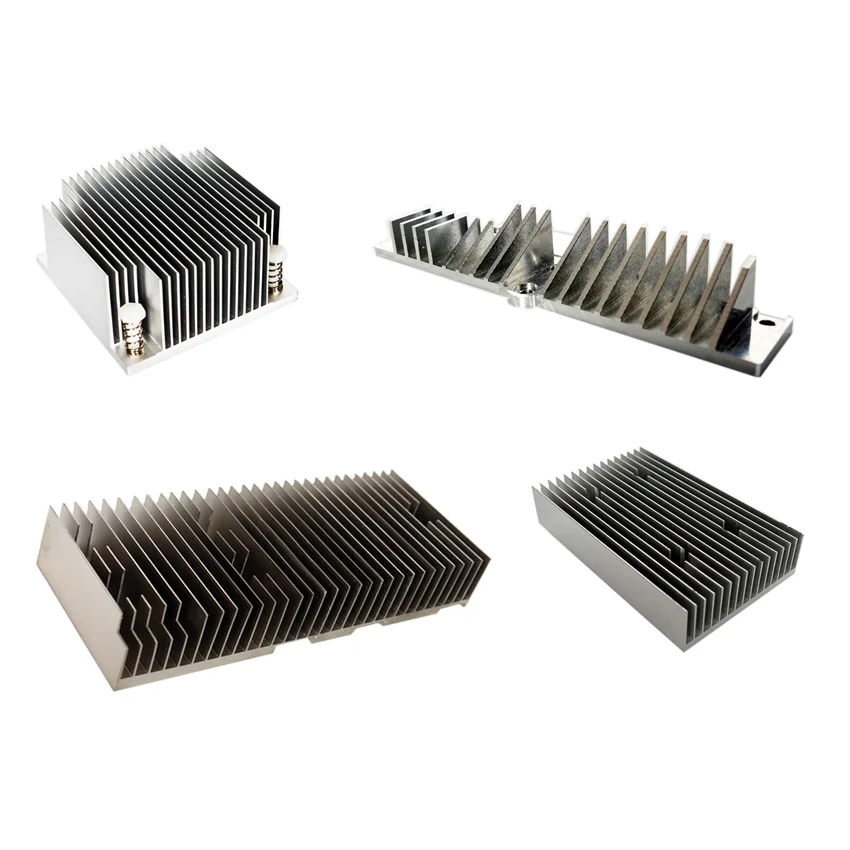
As electronic devices become more powerful and compact, the demand for reliability and performance is ever-increasing. One crucial factor that directly impacts electronics reliability is thermal management. Without proper thermal solutions, devices can suffer from reduced performance, shorter lifespans, and even catastrophic failures. This article explores the role of thermal solutions in enhancing the reliability of electronics, discussing both conventional and emerging cooling technologies that are shaping the future of electronic systems.
Overview of Electronics Reliability
Electronic reliability refers to the ability of electronic components and systems to perform consistently under varying conditions over time. As devices operate, they generate heat due to energy losses in the form of resistance, leakage, and other inefficiencies. If this heat is not efficiently managed, it can lead to thermal stress, affecting the integrity of materials and components. Prolonged exposure to high temperatures accelerates wear and tear, diminishing the lifespan and functionality of devices.
The importance of thermal management in electronics reliability cannot be overstated. Effective thermal solutions ensure that devices operate within safe temperature limits, maintaining optimal performance levels and extending the product’s usable life. As technology continues to advance, so too does the need for innovative cooling solutions that can cope with increasingly complex electronic systems.
Understanding Thermal Stress in Electronic Devices
Definition and Sources of Thermal Stress
Thermal stress in electronics arises from temperature fluctuations that occur as devices power on, off or shift between different operational states. These fluctuations cause expansion and contraction of materials, which can result in mechanical stress, cracking, or warping of components. Key sources of thermal stress include:
- Ambient temperature variations: Devices operating in different environments may experience drastic temperature changes.
- Power cycling: Repeated turning on and off of devices subjects them to sudden shifts in temperature.
- Heat generation from internal components: Processors, power transistors, and other components generate significant heat during operation.
Impact of Temperature Fluctuations on Electronic Components
Temperature fluctuations can have a range of detrimental effects on electronic components:
- Reduced lifespan: Components exposed to excessive heat wear out faster, leading to earlier failure.
- Performance degradation: Elevated temperatures reduce the efficiency of semiconductors, lowering device performance.
- Structural damage: Repeated thermal cycling can weaken solder joints and other critical connections, leading to malfunctions.
Addressing these challenges requires effective thermal solutions that manage and dissipate heat efficiently, ensuring electronic reliability over time.
Core Thermal Management Techniques
Overview of Passive vs. Active Cooling Systems
Thermal management systems generally fall into two categories: passive and active cooling.
- Passive cooling systems rely on natural heat dissipation through conduction, convection, or radiation. Heat sinks and thermal interface materials (TIMs) are commonly used in passive cooling to enhance heat flow away from hot components. These systems are simple and energy-efficient but may struggle with high-power devices.
- Active cooling systems, on the other hand, use mechanical methods such as fans or liquid coolers to enhance heat dissipation. These systems are more effective at managing high heat loads but come with additional energy consumption and complexity.
Advances in Heat Sink Technology and Design Optimization
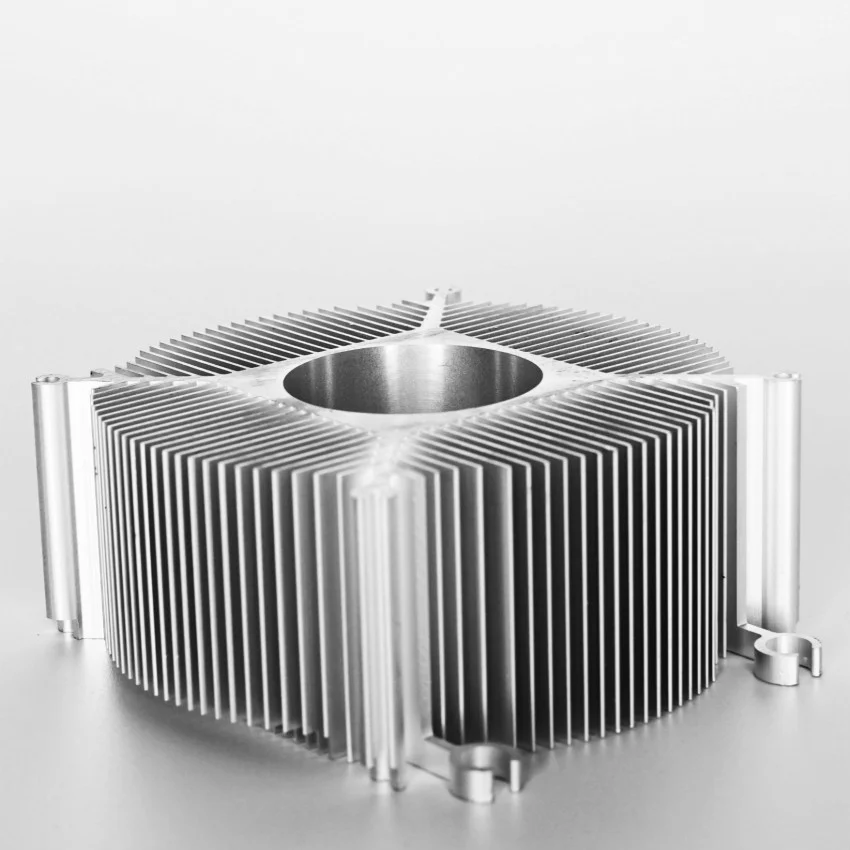
Heat sinks remain a cornerstone of thermal management, particularly in passive cooling systems. Recent advancements in heat sink design include:
- Optimized fin geometry: Enhancements in fin structure allow for more efficient airflow, improving heat dissipation.
- Material innovations: Copper and aluminum alloys remain popular, but advanced materials like graphene are gaining traction for their superior thermal conductivity.
- Compact designs: As electronics become smaller, heat sinks must be designed to fit into increasingly tight spaces without sacrificing performance.
Role of Thermal Interface Materials (TIMs)
Thermal interface materials (TIMs) are critical for ensuring efficient heat transfer between components and heat sinks. TIMs fill the microscopic air gaps between surfaces, allowing for more effective conduction. Innovations in TIM technology, such as phase change materials and nano-enhanced composites, are providing new ways to boost the cooling system impact.
Innovative Cooling Solutions and Their Reliability Benefits
Case Studies on the Use of Phase Change Materials (PCMs) and Hybrid Cooling Systems
Phase change materials (PCMs) offer a novel approach to thermal management by absorbing and releasing heat as they change phases (e.g., from solid to liquid). In hybrid systems, PCMs can be combined with traditional heat sinks or liquid cooling systems to provide enhanced thermal solutions for high-power applications. Case studies have shown that PCMs can significantly improve electronics reliability, especially in environments with fluctuating temperatures.
Analysis of Liquid Cooling and Forced Convection Techniques
Liquid cooling is a powerful technique for managing heat in high-performance systems. By circulating a coolant through heat-generating components, liquid cooling provides superior thermal performance compared to air cooling. Forced convection, which uses fans to increase airflow over heat sinks, is another effective method for dissipating heat in environments where passive cooling alone is insufficient.
Emerging Trends: Synthetic Jet Cooling and Microchannel Coolers
Emerging technologies like synthetic jet cooling and microchannel coolers are pushing the boundaries of thermal management. Synthetic jets, which create high-velocity air streams without moving parts, offer a compact and efficient alternative to traditional fans. Microchannel coolers, which use extremely narrow channels to enhance fluid flow and heat transfer, are being adopted in industries where space is at a premium, such as wearables and portable devices.
Thermal Management for Specific Applications
Automotive Electronics: Challenges and Cooling Strategies
Automotive electronics face extreme temperature ranges, from freezing cold to scorching heat. Thermal solutions in this sector must be robust enough to ensure electronics reliability in harsh conditions. Liquid cooling, heat pipes, and advanced heat sinks are often employed to maintain optimal performance in automotive electronics.
Wearables and Portable Devices: Ensuring Comfort and Longevity
Thermal management in wearables and portable devices focuses on ensuring user comfort and extending device longevity. Passive cooling systems, such as heat spreaders and phase change materials, are commonly used to prevent overheating while maintaining a compact form factor.
High-Power Electronics: Custom Solutions for Heat Dissipation
High-power electronics, such as those used in data centers and industrial applications, generate significant amounts of heat. Custom cooling solutions, including liquid immersion cooling and advanced heat exchangers, are critical for maintaining electronics reliability in these high-demand environments.
Modeling and Simulation in Thermal Management
Importance of Computational Fluid Dynamics (CFD) and Thermal Modeling
Modeling and simulation tools like computational fluid dynamics (CFD) play a crucial role in designing effective thermal management systems. By simulating airflow, heat transfer, and temperature distribution, engineers can predict potential issues and optimize designs before physical prototypes are built. CFD and thermal modeling also help in reducing development costs and improving overall electronics reliability.
How Simulations Predict and Enhance Component Reliability
Simulations allow for early detection of thermal hotspots, which can lead to failures if not addressed. By identifying these areas, designers can implement targeted cooling solutions that ensure components remain within safe operating temperatures, thereby enhancing long-term reliability.
Future Directions in Thermal Management Technology
Innovations on the Horizon: Nano-Enhanced Coolants and Metamaterials
The future of thermal management is likely to be shaped by new materials and technologies. Nano-enhanced coolants, which incorporate nanoparticles into traditional cooling fluids, offer increased thermal conductivity and heat capacity. Similarly, metamaterials, engineered to have unique thermal properties, are being explored for their potential to revolutionize heat transfer.
Sustainable and Energy-Efficient Cooling Technologies
As energy efficiency becomes a greater priority, the development of sustainable thermal solutions is gaining momentum. Technologies such as thermoelectric cooling, which converts heat into electricity, and passive radiative cooling, which emits heat as infrared radiation, are showing promise for reducing energy consumption in cooling systems.
In conclusion, effective thermal management is essential for maintaining electronics reliability in modern devices. From traditional heat sinks and liquid cooling systems to emerging technologies like phase change materials and synthetic jets, the evolution of thermal solutions is ensuring that electronic devices continue to perform reliably even under extreme conditions. For businesses and individuals seeking cutting-edge thermal management solutions, PT Heat Sink is at the forefront, offering innovative products that meet the diverse needs of today’s electronic systems.
FAQs
1. How does thermal management affect electronics reliability?
Thermal management helps prevent overheating, which can degrade components and reduce performance, ultimately enhancing the reliability and lifespan of electronic devices.
2. What are the key differences between passive and active cooling systems?
Passive cooling relies on natural heat dissipation through conduction and convection, while active cooling uses mechanical methods like fans or liquid coolers to manage heat more effectively.
3. What role do thermal interface materials (TIMs) play in thermal solutions?
TIMs improve heat transfer between components and heat sinks by filling microscopic air gaps, ensuring more efficient cooling.
4. Are there specific cooling challenges for automotive electronics?
Yes, automotive electronics often operate in extreme temperatures, requiring robust cooling systems like liquid cooling and heat pipes to maintain reliability.
5. What kind of thermal solutions does PT Heat Sink offer?
PT Heat Sink provides a range of advanced thermal management products, from heat sinks to innovative cooling technologies, designed to enhance the reliability and performance of electronic devices.