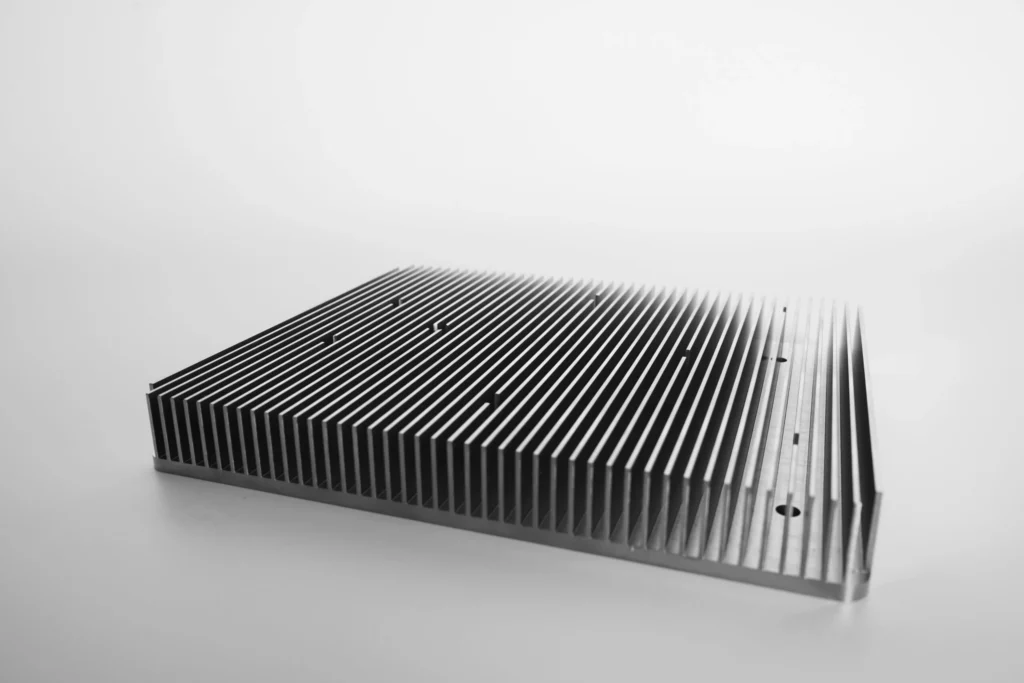
In industrial settings, efficient thermal management is crucial to ensure the longevity and performance of electronic components. As electronic devices continue to shrink in size while increasing in power, the challenge of managing heat effectively becomes more pronounced. Heat sinks are indispensable tools in this battle against overheating, helping to dissipate excess heat and maintain optimal operating temperatures.
Choosing the right heat sink is not just about ensuring the survival of your equipment but also about optimizing efficiency and reducing long-term costs. This article will guide you through the essential factors to consider when selecting the appropriate heat sink for your industrial application.
Understanding the Basics of Heat Sinks
How Heat Sinks Work: Conduction, Convection, and Radiation
To grasp the importance of heat sinks, it’s vital to understand the basic principles of heat transfer: conduction, convection, and radiation.
- Conduction: This is the transfer of heat through a material, moving from a hotter region to a cooler one. In heat sinks, conduction occurs when heat is absorbed from the electronic component and transferred to the heat sink material.
- Convection: This refers to the transfer of heat through a fluid medium (like air or liquid). In the context of heat sinks, convection is responsible for moving heat away from the heat sink into the surrounding environment. This process can be passive (natural air movement) or active (forced air through fans).
- Radiation: Heat transfer via electromagnetic waves. While conduction and convection are the primary methods of heat dissipation in heat sinks, radiation also plays a role, especially in environments with minimal airflow.
Overview of Thermal Resistance and Its Importance
Thermal resistance is a key concept when discussing heat sinks. It measures the heat sink’s ability to resist the flow of heat from the electronic component to the surrounding environment. Expressed in degrees Celsius per watt (°C/W), lower thermal resistance indicates a more efficient heat sink. Properly calculating thermal resistance is essential to ensuring that your heat sink can handle the heat load of your application without allowing temperatures to rise to damaging levels.
Types of Heat Sinks: Passive vs. Active
Heat sinks come in two primary types: passive and active.
- Passive Heat Sinks: These rely on natural convection and radiation to dissipate heat. They have no moving parts, making them highly reliable and maintenance-free. However, they may not be sufficient for high-power applications where more aggressive cooling is required.
- Active Heat Sinks: These incorporate fans or other mechanical devices to force air or liquid over the heat sink, increasing heat dissipation. While more effective in managing high heat loads, active heat sinks are more complex and may require regular maintenance.
Key Factors to Consider When Selecting a Heat Sink
Thermal Performance: How to Calculate the Required Thermal Resistance
The first step in heat sink selection is determining the required thermal resistance. To calculate this, you need to know the maximum allowable junction temperature of your electronic component and the ambient temperature of your environment. Subtract the ambient temperature from the junction temperature to find the maximum temperature rise. Then, divide this by the power dissipation of your component. The result gives you the maximum thermal resistance your heat sink can have while still keeping your component within safe operating temperatures.
Material Selection: Pros and Cons of Different Materials
The material of your heat sink significantly impacts its performance. The two most common materials are aluminum and copper.
- Aluminum: Lightweight and cost-effective, aluminum is the most popular material for heat sinks. It provides a good balance of thermal conductivity and ease of manufacturing, making it ideal for a wide range of applications.
- Copper: With higher thermal conductivity than aluminum, copper is excellent for applications requiring superior heat dissipation. However, copper is more expensive and heavier, which can be a drawback in some designs.
When to Choose Aluminum Over Copper and Vice Versa
Aluminum is typically chosen for industrial heat sinks where weight and cost are primary concerns. Copper is preferred in scenarios where maximum heat dissipation is necessary, and the additional weight and cost are justified by the performance benefits.
Fin Design, Surface Area, and Heat Sink Orientation
The design of the heat sink plays a critical role in its efficiency. Key factors include:
- Fin Design: The shape and orientation of fins on a heat sink increase its surface area and, consequently, its ability to dissipate heat. Common fin designs include straight, pin, and flared fins, each offering different benefits depending on the application.
- Surface Area: More surface area generally equals better heat dissipation. This can be achieved through the use of fins or by increasing the overall size of the heat sink.
- Orientation: The positioning of the heat sink can affect its performance, especially in passive designs. Ensuring that fins are aligned to maximize airflow (whether natural or forced) is essential for optimal performance.
How Operating Environments Affect Heat Sink Performance
The environment in which your heat sink operates will influence its performance. Factors such as ambient temperature, airflow, and space constraints must be considered. For instance, in high-temperature environments, a heat sink may need to be larger or made from a more thermally conductive material. In areas with limited airflow, passive heat sinks might need to be replaced with active ones to ensure adequate cooling.
Cost Considerations: Balancing Performance with Budget Constraints
While it might be tempting to opt for the most efficient or high-performance heat sink available, it’s essential to balance performance with cost. Consider the long-term savings a slightly more expensive but more efficient heat sink might offer, especially in terms of reduced energy consumption and prolonged component life.
Types of Heat Sinks and Their Applications
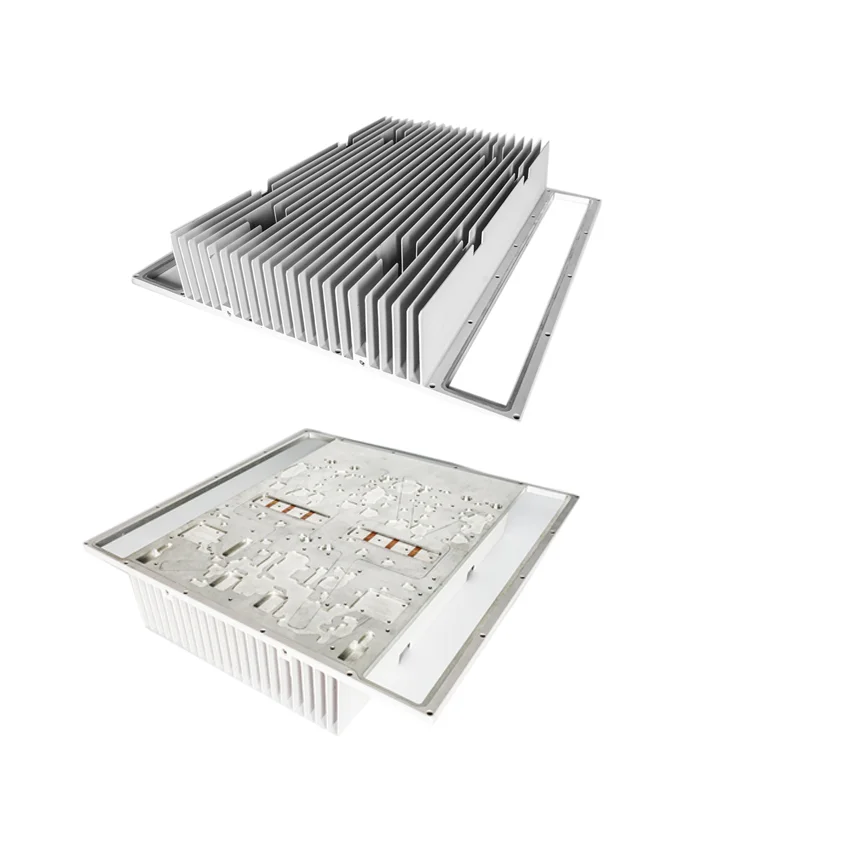
Extruded aluminum heat sinks are among the most commonly used due to their versatility and cost-effectiveness. They are manufactured by pushing aluminum through a die to create specific shapes, making them ideal for a variety of applications, from consumer electronics to industrial machinery. These heat sinks are especially effective in moderate power applications where weight and cost are critical factors.
Bonded-Fin Heat Sinks
When dealing with high-power applications, bonded-fin heat sinks are often the preferred choice. These heat sinks are constructed by bonding fins to a base, usually with a thermal adhesive, creating a much larger surface area for heat dissipation. This design makes them suitable for applications like power converters and industrial control systems, where high thermal loads are common.
Skived, Forged, and Die-Cast Heat Sinks: When and Why to Use Them
- Skived Heat Sinks: Manufactured by skiving, or slicing, thin layers from a solid block of material, these heat sinks offer excellent thermal performance due to their one-piece construction. They are ideal for applications requiring high reliability, such as automotive and aerospace industries.
- Forged Heat Sinks: These are created through a forging process that compresses material into a dense, uniform structure. Forged heat sinks are known for their durability and are often used in harsh industrial environments where mechanical strength is a priority.
- Die-Cast Heat Sinks: Made by forcing molten metal into a mold, die-cast heat sinks offer high design flexibility, allowing for complex shapes and features. They are commonly used in LED lighting and automotive electronics, where specific thermal and mechanical properties are required.
CNC Machined Heat Sinks
CNC machined heat sinks are tailored for high-tech industries where precision is paramount. These heat sinks are made to exact specifications using computer-controlled machining tools, ensuring that they meet the stringent demands of applications like aerospace components and high-performance computing.
Case Studies: Examples from Different Industries
- Automotive: Skived heat sinks are used in electric vehicles to manage the heat generated by batteries and power electronics.
- Aerospace: CNC machined heat sinks are critical in aerospace applications where precise thermal management is required for sensitive instruments.
- LED Lighting: Die-cast heat sinks are preferred for their ability to dissipate heat in compact, high-efficiency LED modules.
Guide to Choosing the Right Heat Sink
Step 1: Determine Your Thermal Requirements
To choose the right heat sink, start by calculating the maximum junction temperature your component can tolerate. Subtract the ambient temperature from this value to determine the maximum allowable temperature rise. Then, calculate the required thermal resistance by dividing the temperature rise by the power dissipation of your component.
Step 2: Analyze Your Environment
Consider the environment where the heat sink will operate. Factors such as airflow, space constraints, and ambient temperature will impact your choice. In environments with limited airflow, you might need an active heat sink, whereas passive heat sinks might suffice in cooler, well-ventilated areas.
Step 3: Compare Material and Design Options
Evaluate different materials and designs based on your application’s needs. Aluminum might be sufficient for most industrial applications, but if you’re dealing with high heat loads, copper or a combination of materials might be necessary. Similarly, choose a fin design that maximizes heat dissipation while considering space and airflow constraints.
Step 4: Cost vs. Performance Analysis
After considering the thermal requirements, environmental factors, and material and design options, the final step in choosing heat sinks is performing a thorough cost vs. performance analysis. This step ensures that you’re not only selecting a heat sink that meets your thermal needs but also one that aligns with your budget constraints and long-term operational goals.
Evaluate Initial Costs
Begin by evaluating the initial costs associated with each heat sink option. Aluminum heat sinks are generally more affordable than copper, making them a popular choice for cost-sensitive projects. However, if your application demands superior thermal performance, the higher initial cost of a copper heat sink may be justified. For example, a bonded-fin heat sink made of copper could cost significantly more than an aluminum alternative, but its higher thermal conductivity might be necessary for your specific application, especially in high-power environments.
Consider Long-Term Savings
While it’s tempting to choose the least expensive option upfront, it’s important to consider the long-term implications of your choice. A more efficient heat sink might reduce energy costs by maintaining optimal operating temperatures, thereby extending the lifespan of your electronic components and reducing maintenance costs. For instance, a skived heat sink, despite its higher production cost, offers enhanced durability and reliability, which can translate into long-term savings in critical applications like automotive or aerospace.
Assess Maintenance and Operational Costs
Active heat sinks, which incorporate fans or other moving parts, may have lower upfront costs compared to passive solutions that require more material or advanced manufacturing techniques. However, active heat sinks come with higher operational costs due to their energy consumption and potential maintenance needs. Over time, the costs of replacing or repairing fans can add up, especially in environments where downtime is costly. In contrast, passive heat sinks might have higher initial costs due to the need for larger or more complex designs, but they typically require little to no maintenance, offering cost benefits over the life of the equipment.
Weigh the Performance Benefits
Finally, consider the performance benefits that each heat sink option provides relative to its cost. If your application operates in a high-temperature environment with significant thermal loads, investing in a high-performance heat sink, such as a forged or CNC machined heat sink, might be essential. These options, while more expensive, offer superior thermal management capabilities, ensuring that your components operate within safe temperature ranges and minimizing the risk of overheating and failure.
Making the Final Decision
To make an informed decision, compare the total cost of ownership (TCO) for each heat sink option. This includes the initial purchase price, installation costs, energy consumption, maintenance requirements, and potential savings from prolonged equipment life and reduced downtime. By taking a holistic view of both short-term expenses and long-term benefits, you can select the heat sink that offers the best balance of performance and cost-effectiveness for your industrial application.
Common Mistakes to Avoid When Selecting a Heat Sink
Overlooking Environmental Factors
One of the most common mistakes in heat sink selection is failing to account for environmental conditions. Heat sinks that perform well in controlled environments may fail in high-temperature or low-airflow situations. Always consider the specific environmental conditions of your application to avoid thermal management failures.
Miscalculating Thermal Resistance
Another frequent error is the miscalculation of thermal resistance. Underestimating the required thermal resistance can lead to inadequate cooling, causing components to overheat. It’s crucial to accurately calculate the thermal resistance needed for your application and select a heat sink that meets or exceeds this requirement.
Ignoring the Importance of Proper Installation
The performance of a heat sink is not just about its design and materials but also about how well it is installed. Neglecting the application of thermal interface materials (TIMs), such as thermal grease or pads, can result in poor heat transfer from the component to the heat sink, significantly reducing its effectiveness. Ensure that your heat sink is properly installed with the correct TIM to maximize its cooling efficiency.
Choosing the right heat sink is a critical step in ensuring the reliability and efficiency of your industrial applications. By carefully considering thermal performance, material selection, design, environmental factors, and cost, you can select a heat sink that not only meets your technical requirements but also aligns with your budgetary constraints.
PT heatsink understands the complexities involved in heat sink selection and offers a wide range of solutions tailored to meet the diverse needs of industrial applications. Our expertise in thermal management ensures that you receive a heat sink that delivers optimal performance, helping to extend the life of your equipment and reduce operational costs.
FAQ
- What is the most critical factor in choosing a heat sink?
The most critical factor is the thermal resistance, as it determines how effectively the heat sink can dissipate heat from the component to the environment. - How do I know if my heat sink is performing optimally?
You can monitor the operating temperature of your component under load. If it remains within the specified safe range, the heat sink is performing as expected. - Can I customize a heat sink for my specific needs?
Yes, customized heat sinks can be designed to meet specific thermal requirements, environmental conditions, and space constraints. Customization allows for optimizing performance based on your unique application needs. - What custom solutions does Ptheatsink offer?
Ptheatsink provides custom heat sinks tailored to specific industrial needs, including various materials and designs, ensuring optimal performance for your applications.