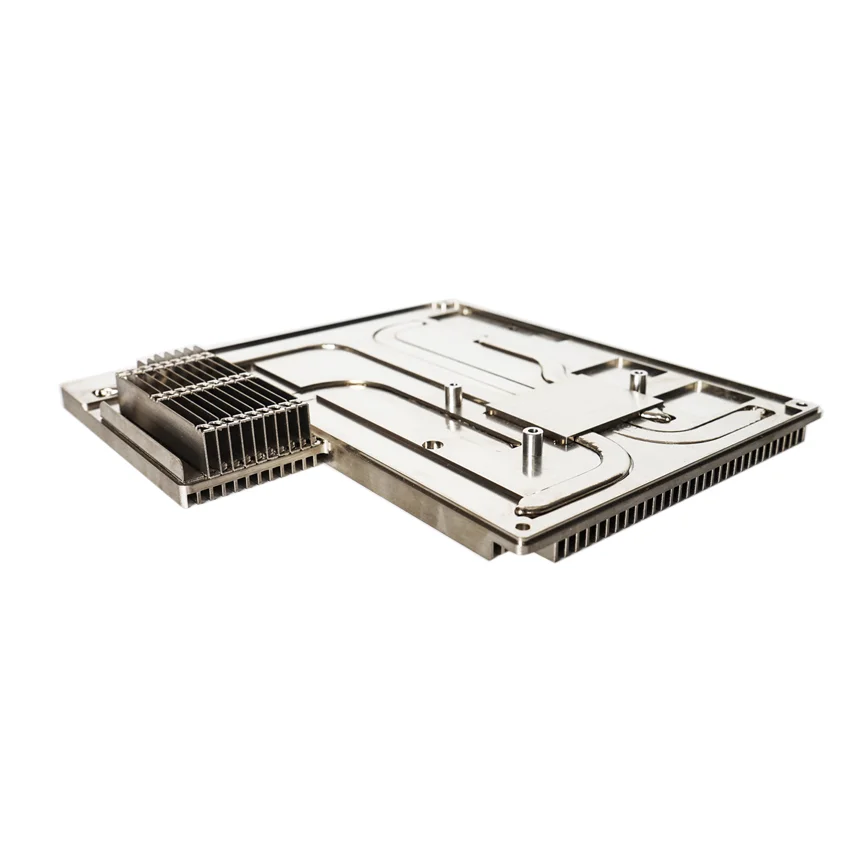
Heat sinks have long been at the forefront of cooling technology trends, playing a critical role in maintaining the performance and longevity of electronic devices. As technology advances, the demand for more efficient thermal management solutions has driven innovation in heat sink design. These innovations aim to enhance heat dissipation, improve energy efficiency, and reduce material costs while meeting the growing needs of industries such as consumer electronics, automotive, and renewable energy.
In this article, we will explore the latest trends shaping the future of heat sink design and application, examining how advanced materials, new manufacturing techniques, and integration with renewable technologies are changing the landscape.
Advanced Materials in Heat Sink Design
The choice of materials plays a crucial role in determining the efficiency of a heat sink. Traditional materials like aluminum and copper have been widely used due to their high thermal conductivity and relatively low cost. However, as the performance demands of modern electronics increase, there is a growing interest in novel materials that offer superior heat dissipation properties without the bulk or weight of traditional materials.
Carbon Nanotubes
Carbon nanotubes (CNTs) are emerging as a game-changer in heat sink design. These nanomaterials offer extremely high thermal conductivity—up to ten times greater than copper—while being lightweight and highly flexible. Carbon nanotubes are also resistant to thermal degradation, making them ideal for high-performance electronics that require long-lasting thermal solutions.
One challenge with carbon nanotubes is their cost and scalability. While CNTs offer impressive thermal performance, the technology is still evolving to make them a more commercially viable solution for mass production.
Graphene
Another promising material is graphene, a two-dimensional carbon sheet known for its remarkable thermal conductivity. Graphene-based heat sinks have the potential to dissipate heat more efficiently than conventional metal-based heat sinks while being much lighter. The use of graphene in heat sink application is particularly advantageous in compact devices where weight and space are critical considerations, such as smartphones and wearables.
In addition to its thermal properties, graphene is highly flexible, making it suitable for applications in flexible electronics and devices where design versatility is a key factor.
Emerging Design Techniques
As new materials are introduced, the design of heat sinks is also evolving to maximize thermal efficiency. Beyond traditional finned and extruded heat sinks, designers are now employing cutting-edge techniques that optimize heat dissipation while minimizing the material used.
Topology Optimization
Topology optimization is an advanced design approach that uses computational algorithms to generate an optimal heat sink structure based on the cooling requirements of the system. By analyzing the heat load and distribution, topology optimization can create complex designs that maximize surface area while minimizing material waste.
One of the key benefits of topology optimization is its ability to create lightweight, highly efficient heat sinks that are tailored to specific applications. This design technique is especially useful in aerospace and automotive industries, where weight reduction is critical to improving performance and fuel efficiency.
Fractal Geometries
Fractal geometries, inspired by naturally occurring patterns, are another emerging trend in heat sink design. Fractals are self-repeating structures that can create a larger surface area for heat dissipation without increasing the overall size of the heat sink. These designs are particularly beneficial in environments with limited space, such as compact electronic devices and high-density server racks.
In one recent case study, a company implementing fractal-based heat sinks in their data center cooling systems saw a 20% improvement in thermal performance, allowing for more efficient cooling in smaller spaces. This design approach is also being explored in other high-performance applications, including electric vehicle battery cooling systems.
Innovations in Manufacturing Processes
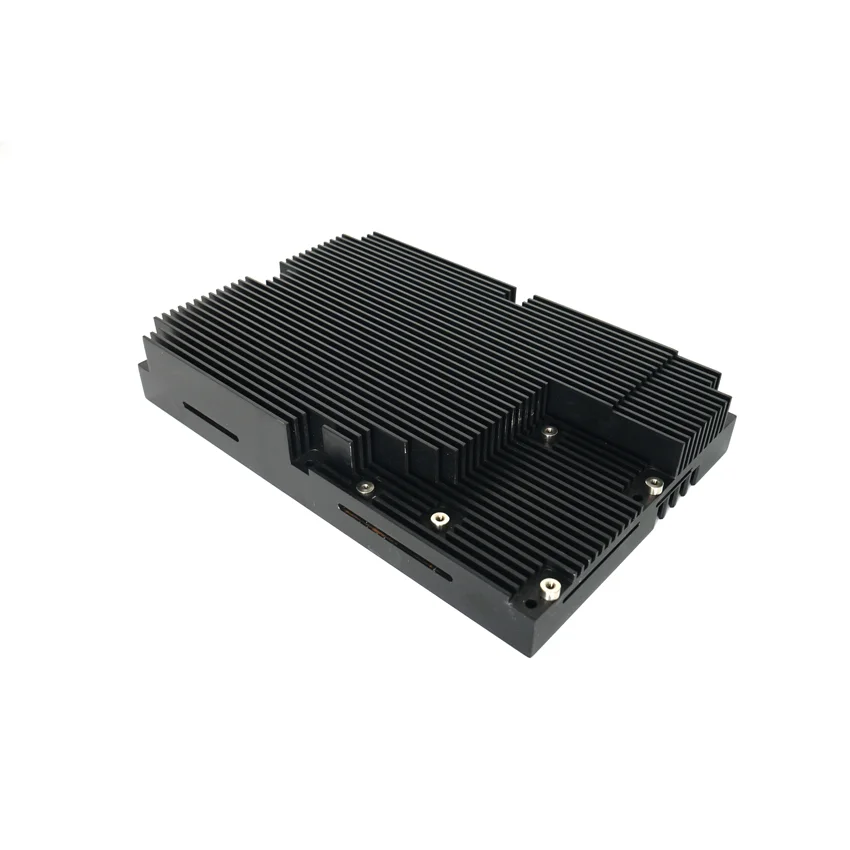
The evolution of heat sink technology is not only driven by new materials and design techniques but also by advancements in manufacturing processes. These innovations are enabling more complex, precise, and efficient heat sink designs that were previously impossible using traditional methods.
Additive Manufacturing (3D Printing)
Additive manufacturing, commonly known as 3D printing, is revolutionizing the production of heat sinks. Unlike traditional methods such as casting or extrusion, 3D printing allows for the creation of highly complex, customized heat sink structures that can be optimized for specific cooling requirements. This level of customization is particularly valuable in industries like aerospace and medical devices, where standard heat sink designs may not provide adequate thermal management.
3D printing also reduces material waste, as only the necessary amount of material is used in the manufacturing process. This results in lighter, more efficient heat sinks that are ideal for applications where weight and space are key constraints.
Precision Machining and Laser Etching
Advances in precision machining and laser etching technologies are also contributing to the development of more efficient heat sinks. These techniques allow manufacturers to create intricate cooling channels and surface textures that enhance the overall heat transfer capabilities of the heat sink. Precision machining enables the production of ultra-thin fins and microstructures that increase the heat sink’s surface area without increasing its size or weight.
Integration with Renewable Technologies
As industries worldwide shift toward more sustainable practices, heat sink designs are being optimized for integration with renewable energy technologies. Whether it’s enhancing the efficiency of solar panels or improving heat dissipation in wind turbines, heat sink application in renewable energy is a growing area of focus.
Solar Panels
In solar energy systems, heat sinks play a critical role in preventing overheating of photovoltaic cells, which can reduce the overall efficiency of energy conversion. By incorporating advanced heat sinks that dissipate excess heat, solar panels can operate at optimal temperatures, resulting in greater energy production over time.
Wind Turbines
Similarly, heat sinks are being designed for use in wind turbines to manage the heat generated by the electrical components housed in the nacelle. Cooling these components is essential for maintaining the performance and reliability of the turbine. Innovations in heat sink materials and design, such as those using graphene and fractal geometries, are helping to improve the thermal efficiency of wind turbines, ultimately contributing to more reliable and sustainable energy generation.
Future Trends and Predictions
As cooling technology trends continue to evolve, several exciting advancements are on the horizon for heat sink design. The future of heat sink technology will likely be driven by new materials, more efficient designs, and the integration of AI and machine learning for predictive performance modeling.
Nano-Enhanced Materials
Nano-enhanced materials, such as carbon nanofibers and metal-organic frameworks (MOFs), are showing great potential for use in next-generation heat sinks. These materials offer even higher thermal conductivity than carbon nanotubes and graphene, enabling faster heat dissipation in increasingly compact and powerful devices. The development of these materials could lead to a new class of heat sinks that are lighter, more efficient, and capable of handling higher heat loads.
AI and Machine Learning for Predictive Performance
As the complexity of heat sink designs increases, so too does the need for advanced modeling and simulation techniques. AI and machine learning are playing an increasingly important role in predicting the performance of heat sinks under various conditions. By analyzing vast amounts of data, these technologies can optimize heat sink designs in real-time, leading to more efficient and reliable cooling solutions.
For example, AI-driven predictive modeling can identify potential thermal hotspots in electronic devices and recommend design modifications before the heat sink is even manufactured. This approach not only improves the overall efficiency of the cooling system but also reduces development time and costs.
The continuous innovation in heat sink design is essential for meeting the growing thermal management needs of modern electronics and renewable energy systems. From the use of advanced materials like carbon nanotubes and graphene to the adoption of new design techniques like topology optimization and fractal geometries, the future of heat sinks is brighter and more efficient than ever before.
As businesses explore cutting-edge solutions for their thermal management challenges, partnering with experts like PT Heat Sink can provide access to the latest advancements in heat sink technology, ensuring that your systems stay cool and perform optimally.
FAQs
1. What materials are best for heat sink design?
Traditional materials like aluminum and copper are still widely used due to their high thermal conductivity. However, advanced materials like carbon nanotubes and graphene offer superior thermal performance and are being used in cutting-edge applications.
2. How do advanced manufacturing techniques impact heat sink performance?
Innovations like 3D printing and precision machining allow for more complex and optimized heat sink designs, resulting in improved thermal management and efficiency.
3. Can heat sinks be used in renewable energy systems?
Yes, heat sinks are increasingly being integrated into renewable energy technologies, such as solar panels and wind turbines, to manage excess heat and improve efficiency.
4. What are fractal geometries in heat sink design?
Fractal geometries are self-repeating structures that create a larger surface area for heat dissipation without increasing the overall size of the heat sink. This design approach enhances thermal performance in compact devices.