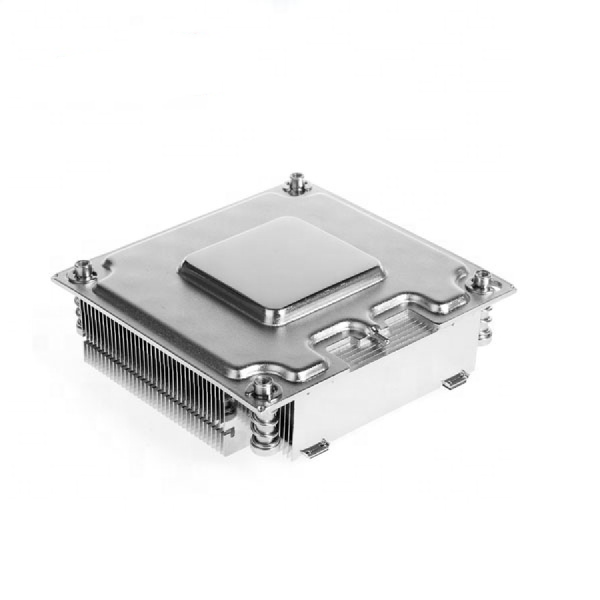
In the high-stakes world of aerospace engineering, maintaining the optimal temperature of components is critical to ensuring the safety, reliability, and performance of aircraft and spacecraft. From the early days of aviation to the cutting-edge technologies employed in modern thermal management aerospace applications, thermal management has evolved significantly.
This article explores the journey of thermal management in aerospace, highlighting the challenges faced, innovations introduced, and future trends that will shape this vital aspect of aerospace engineering.
Early Thermal Management Techniques
Challenges in Heat Management
The dawn of aerospace engineering brought with it a host of challenges, chief among them being the management of heat generated by aircraft engines and other components. Early aircraft, often constructed from wood and fabric, encountered minimal issues with overheating due to their relatively low speeds and power outputs. However, as engines became more powerful and airframes more advanced, the need for effective thermal management aerospace solutions became apparent.
First-Generation Cooling Solutions, Natural Convection and Basic Materials
The earliest solutions for managing heat in aircraft were rudimentary, relying heavily on natural convection. Engine cowlings were designed to maximize airflow over the engine, allowing the heat to dissipate naturally. Materials like aluminum, prized for its lightweight and good thermal conductivity, were introduced to improve heat dissipation. However, these first-generation cooling methods were far from perfect, often leading to overheating and performance issues in more demanding flight conditions.
Thermal Management in WWII Aircraft
World War II marked a significant period of innovation in aerospace engineering, with thermal management taking center stage. Aircraft such as the Supermarine Spitfire and the North American P-51 Mustang were equipped with increasingly powerful engines, leading to substantial heat generation. To combat this, engineers developed more sophisticated cooling systems, including liquid-cooled engines and more effective radiator designs. The lessons learned during this period laid the groundwork for future advancements in aerospace thermal management.
The Jet Age and the Rise of Advanced Cooling
The Need for Sophisticated Cooling
The advent of jet propulsion in the mid-20th century revolutionized aviation but also introduced new challenges in thermal management aerospace. Jet engines operate at much higher temperatures than piston engines, requiring more sophisticated cooling systems to prevent overheating and ensure reliability.
Development of Heat Sinks and Thermal Barriers
As jet engines became more prevalent, so too did the need for more advanced thermal management solutions. Heat sink selection became a critical aspect of aerospace design, with engineers developing more effective heat sinks to manage the intense heat generated by jet engines. Thermal barrier coatings (TBCs) were also introduced during this period, providing an additional layer of protection against the extreme temperatures encountered in jet engines. These coatings, often made from ceramic materials, helped to extend the lifespan of engine components and improve overall performance.
Alloys and Composites
The development of new materials played a crucial role in advancing thermal management during the jet age. Alloys such as titanium and nickel-based superalloys were introduced, offering improved thermal conductivity and resistance to high temperatures. Additionally, composite materials, which combine different materials to enhance specific properties, became more common. These innovations in material science significantly improved the effectiveness of thermal management systems in aerospace applications.
Modern Thermal Management Systems in Aerospace
Thermal Interface Materials (TIMs)
In modern aerospace engineering, Thermal Interface Materials (TIMs) are indispensable components of thermal management systems. TIMs are used to fill the microscopic gaps between heat-generating components and heat sinks, ensuring efficient heat transfer. Recent innovations in TIMs, such as the use of carbon nanomaterials, have further enhanced their performance, allowing for even more effective cooling in high-demand aerospace applications.
Active vs. Passive Cooling Systems
Today, aerospace engineers employ both active and passive cooling systems, depending on the specific requirements of the application. Active cooling systems use mechanisms like fans or liquid cooling to actively dissipate heat, making them ideal for high-power components such as avionics and radar systems. In contrast, passive cooling systems rely on natural convection and conduction, using industrial heat sinks and heat pipes to manage heat without the need for moving parts. The choice between active and passive cooling often depends on factors such as power density, weight, and the specific operational environment.
The Thermal Management System of the Boeing 787
The Boeing 787 Dreamliner, a modern marvel of aerospace engineering, integrates a complex thermal management system that exemplifies the advancements made in this field. The aircraft uses a combination of heat sinks, liquid cooling, and advanced TIMs to manage the heat generated by its high-efficiency engines and extensive electronic systems. The 787’s thermal management system is a testament to the importance of integrating multiple cooling technologies to ensure optimal performance and reliability.
The Impact of Electrification on Thermal Management
Electric Aircraft
The shift towards electrification in aerospace is driving the need for new and innovative thermal management solutions. Electric aircraft, which rely on electric motors and batteries, generate significant amounts of heat, particularly in the high-power-density systems required for propulsion. Managing this heat is critical to ensuring the safety and efficiency of these next-generation aircraft.
Challenges of High Power Density
High power density is one of the primary challenges in thermal management aerospace. As components become smaller and more powerful, the amount of heat generated per unit of volume increases, making it more difficult to dissipate this heat effectively. This challenge is particularly acute in electric aircraft, where battery and motor cooling are critical to performance and safety.
Emerging Solutions and Cooling Technologies
To address these challenges, aerospace engineers are developing cutting-edge cooling technologies. These include advanced industrial heat sinks with optimized fin designs, liquid cooling systems that use advanced heat exchangers, and even phase-change materials that absorb and dissipate heat as they change state. These emerging solutions are helping to push the boundaries of what is possible in aerospace thermal management, enabling the development of more efficient and reliable electric aircraft.
Future Trends and Innovations in Thermal Management
Nanotechnology and Advanced Materials
Nanotechnology is poised to revolutionize thermal management aerospace. Nanomaterials, such as carbon nanotubes and graphene, offer extraordinary thermal conductivity and could be used to create more efficient heat sinks aerospace and TIMs. Additionally, the development of advanced composites that combine these nanomaterials with traditional materials could lead to even greater improvements in thermal management performance.
AI and Computational Fluid Dynamics (CFD): Enhancing Design and Efficiency
The integration of AI and Computational Fluid Dynamics (CFD) into the design process is another exciting trend in aerospace thermal management. AI can be used to optimize the design of cooling systems, predicting how different materials and configurations will perform under various conditions. CFD simulations allow engineers to model complex fluid flows and heat transfer processes, enabling them to design more efficient and effective thermal management systems.
Sustainability Considerations, Balancing Performance and Environmental Impact
As the aerospace industry continues to prioritize sustainability, developing thermal management solutions that are both efficient and environmentally friendly is becoming increasingly important. This includes using materials that are less harmful to the environment, designing systems that reduce energy consumption, and developing cooling technologies that can be easily recycled or repurposed.
The evolution of thermal management aerospace has been a journey marked by significant advancements in materials, design, and technology. From the early days of aviation, where simple cooling methods were employed, to the sophisticated thermal management systems used in modern aircraft, the field has come a long way. As we look to the future, innovations in nanotechnology, AI, and sustainable design will continue to shape the way we manage heat in aerospace applications.
PT heatsink is at the forefront of these advancements, offering cutting-edge thermal management solutions tailored to the unique needs of the aerospace industry. By leveraging the latest technologies and materials, ptheatsink helps ensure that modern aircraft operate safely and efficiently, even in the most demanding environments.
FAQ
- Why is thermal management crucial in aerospace engineering?
Thermal management ensures that all components in an aircraft or spacecraft operate within safe temperature ranges, maintaining safety, reliability, and performance, especially in extreme environments. - What are the biggest challenges in cooling modern aircraft?
The main challenges include managing heat from powerful engines and electronics, addressing high power densities in electric aircraft, and developing lightweight, efficient, and sustainable cooling solutions. - How does ptheatsink contribute to aerospace thermal management?
ptheatsink offers advanced solutions using the latest materials and technologies, tailored to meet the unique demands of modern aerospace applications for optimal performance and reliability. - What are the primary methods used to cool aircraft components?
Aircraft components are cooled mainly through convection, conduction, and radiation, ensuring heat is effectively dissipated to maintain proper operation. - Why is maintaining optimal temperatures in aircraft systems important?
Keeping systems at optimal temperatures prevents overheating, ensuring the safety, reliability, and performance of the aircraft.