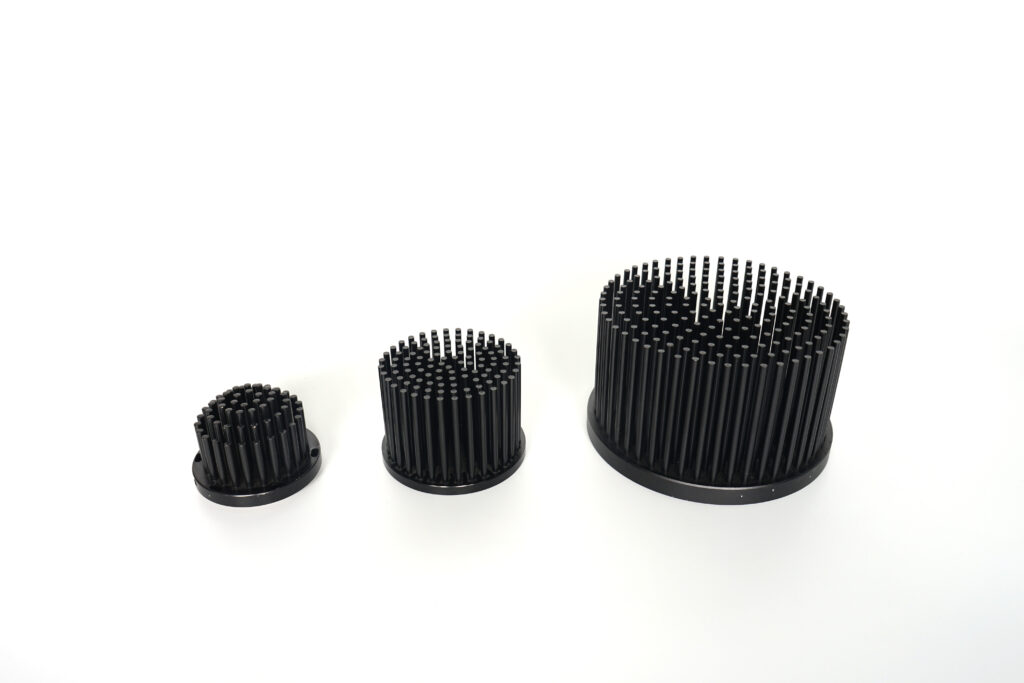
In today’s fast-paced technological environment, managing heat in high-power devices is one of the most critical challenges engineers face. As devices grow more powerful and compact, efficient thermal management becomes paramount to ensure reliability, longevity, and optimal performance. This is where heat sinks, specifically forged heat sinks, play a crucial role. A heat sink is designed to dissipate heat from the device to the surrounding environment, thus preventing overheating and potential damage.
In this article, we’ll explore the efficiency of forged heat sinks, particularly in high-power devices, and how their unique properties make them a superior choice for modern electronics.
Understanding Forged Heat Sinks
Forged heat sinks are created through a manufacturing process known as forging. Forging involves shaping metal using localized compressive forces, typically achieved by hammering, pressing, or rolling. This process offers several benefits over other types of heat sinks, such as extruded, die-cast, and machined heat sinks.
1. Forging Process and Its Benefits: During the forging process, the metal is subjected to high pressure, which results in a heat sink that is stronger and denser compared to those made through other methods. This not only increases the durability of the heat sink but also improves its thermal conductivity. The forging process allows for intricate designs and the ability to achieve thin fin structures, which are essential for efficient heat dissipation.
2. Comparison with Other Types of Heat Sinks: While extruded heat sinks are created by forcing molten metal through a die and die-cast heat sinks are produced by injecting molten metal into molds, both methods have limitations. Extruded heat sinks may lack the design flexibility needed for high-power applications, while die-cast heat sinks can have less structural integrity.
Machined heat sinks, on the other hand, involve cutting or shaping a piece of metal into the desired design, which can be time-consuming and costly. Forged heat sinks offer a balance between structural strength, flexibility in design, and efficient production, making them highly effective for high-power cooling applications.
Key Properties of Forged Heat Sinks
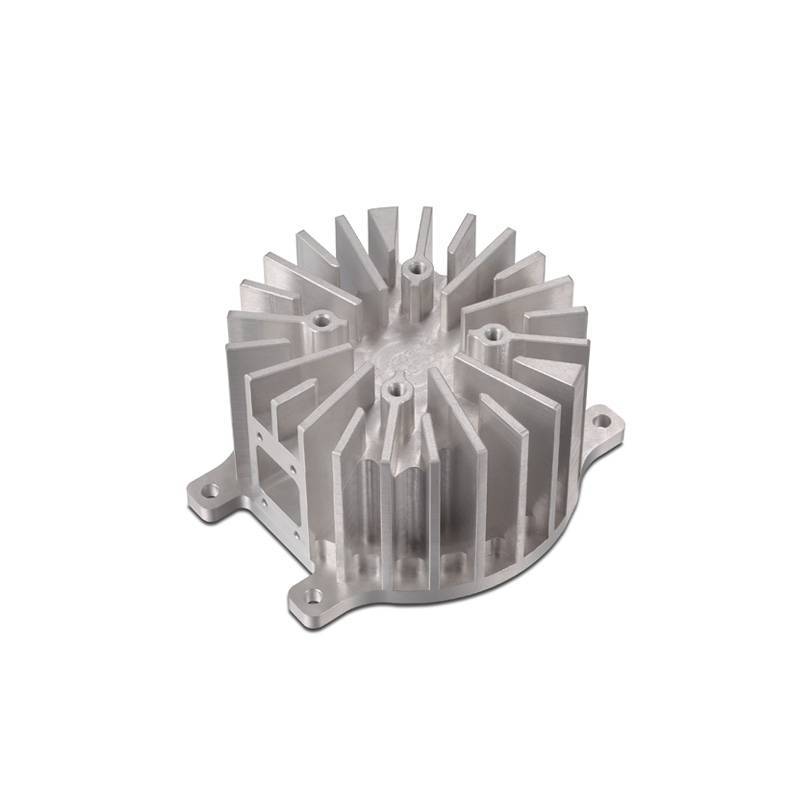
The unique properties of forged heat sinks set them apart from other types of heat sinks, especially when it comes to managing high-power devices.
1. Material Properties: One of the most critical factors in heat sink performance is the material used. Forged heat sinks are typically made from materials like aluminum or copper, both known for their excellent thermal conductivity. Aluminum is lightweight and affordable, while copper offers superior thermal performance. In forged heat sinks, the forging process further enhances the material’s thermal conductivity by eliminating internal voids and imperfections that can reduce heat dissipation efficiency. This makes forged heat sinks more effective at managing heat generated by high-power devices.
2. Design Flexibility: Forged heat sinks offer unparalleled design flexibility. The forging process allows for intricate fin designs that maximize surface area, which is crucial for effective heat dissipation. With more surface area, the heat sink can transfer heat from the device to the air more efficiently, reducing the risk of overheating. Additionally, the forging process allows for precise control over the geometry of the heat sink, ensuring that each part of the device receives adequate cooling.
Advantages of Forged Heat Sinks in High-Power Devices
When it comes to high-power devices, thermal efficiency is paramount. Forged heat sinks offer several advantages that make them particularly well-suited for these applications.
1. Thermal Efficiency: The high thermal conductivity and precise design of forged heat sinks allow for exceptional thermal efficiency. In high-power devices, where heat generation is substantial, this efficiency is critical to maintaining optimal performance and preventing damage. Forged heat sinks can handle higher heat loads compared to their extruded or die-cast counterparts, making them ideal for use in devices like power supplies, LED lighting systems, and telecommunications equipment.
2. Case Studies and Examples: One example of forged heat sinks outperforming other types is in the telecommunications industry. High-power amplifiers used in radio transmission require efficient thermal management to prevent signal degradation. Forged heat sinks have been shown to dissipate heat more effectively in these applications, allowing for more stable signal transmission over long periods.
Another example can be found in electric vehicles, where high-power battery systems need efficient cooling to maintain safety and performance. Forged heat sinks have proven to be reliable in managing the heat generated by these powerful systems.
Design Considerations for Forged Heat Sinks
Designing an efficient forged heat sink requires careful consideration of various factors.
1. Fin Design and Surface Area: The design of the fins plays a crucial role in the heat sink’s ability to dissipate heat. Fins increase the surface area available for heat transfer, which improves overall efficiency. In forged heat sinks, the fin design can be optimized to provide maximum airflow and heat dissipation without increasing the overall size of the heat sink. Additionally, the shape and thickness of the fins can be tailored to suit the specific cooling requirements of the device.
2. Material Selection and Geometric Precision: Choosing the right material for a forged heat sink is essential. Aluminum is often the material of choice due to its lightweight nature and good thermal conductivity. However, for applications where higher thermal performance is required, copper may be preferred. Geometric precision is also critical in ensuring that the heat sink fits perfectly with the device and provides uniform cooling. Forged heat sinks offer the precision needed to meet these demands, making them suitable for complex high-power devices.
Innovations in Forged Heat Sink Technology
As technology continues to evolve, so do the methods used to manufacture heat sinks. Recent advancements in forging technology have led to even more efficient heat sinks for high-power devices.
1. Latest Advancements: One such advancement is the use of computer-aided design (CAD) and computer-aided manufacturing (CAM) systems to create highly detailed heat sink designs. These systems allow engineers to simulate the thermal performance of different designs before they are manufactured, ensuring that the final product offers the best possible cooling efficiency. Additionally, new forging techniques have been developed that allow for thinner and more intricate fins, further improving the heat sink’s ability to dissipate heat.
2. Future Trends: Looking ahead, we can expect to see even more innovations in forged heat sink design. One potential area of improvement is the use of composite materials that combine the thermal conductivity of metals like copper with the lightweight properties of materials like aluminum. This could lead to heat sinks that offer the best of both worlds: high thermal performance and reduced weight. Additionally, advances in additive manufacturing, or 3D printing, may eventually be integrated with forging techniques to create custom heat sinks with even greater design flexibility.
Choosing the Right Forged Heat Sink for Your Needs
When selecting a forged heat sink for a specific application, there are several factors to consider.
1. Factors to Consider: The power requirements of the device, the environment in which it will be used, and the available space for the heat sink all play a role in determining the best option. Engineers must also consider the material of the heat sink, as different materials offer varying levels of thermal conductivity and durability. In high-power cooling applications, it’s essential to select a heat sink that can handle the heat load without compromising the performance of the device.
2. Tools and Resources: For engineers and designers, there are numerous tools and resources available to help select the optimal forged heat sink. Simulation software can be used to model the thermal performance of different heat sink designs, while online databases and catalogs provide detailed specifications for various heat sink options.
Real-World Applications of Forged Heat Sinks
Forged heat sinks are used in a wide variety of industries and devices where efficient thermal management is crucial.
Some of the most common applications for forged heat sinks include telecommunications equipment, power supplies, LED lighting systems, and electric vehicles. In each of these industries, high-power devices generate significant amounts of heat that must be dissipated to prevent damage and maintain performance. Forged heat sinks are also used in medical devices, where precise temperature control is essential for patient safety and device reliability.
Forged heat sinks are critical components in ensuring the efficiency and reliability of high-power devices. Their unique properties, such as enhanced thermal conductivity, design flexibility, and structural strength, make them superior to other heat sink types like extruded or die-cast options. With advancements in forging technology and increasing demand for more powerful electronic devices, forged heat sinks are set to play an even greater role in managing heat effectively.
When choosing a forged heat sink, it’s essential to consider factors like material selection, design precision, and cooling requirements to ensure optimal performance. PT Heat Sink’s offerings are designed to meet the demanding requirements of modern electronic applications, especially those that involve high power. This ensures that each solution not only addresses thermal challenges effectively but also enhances the overall efficiency of the device or system in use.
As innovations in forged heat sink design continue, we can expect to see further improvements in cooling efficiency, making them an even more critical solution for industries that rely on high-performance devices. Whether it’s telecommunications, electric vehicles, or LED lighting, forged heat sinks will remain at the forefront of thermal management solutions for years to come.
FAQs
- What is the main advantage of using forged heat sinks over other types?
Forged heat sinks offer superior thermal efficiency and durability due to their denser structure and design flexibility, making them ideal for high-power applications.
- Are forged heat sinks more expensive than extruded or die-cast heat sinks?
While forged heat sinks may have a higher upfront cost, their improved performance and durability often make them a more cost-effective solution in the long run.
- Can forged heat sinks be customized for specific devices?
Yes, the forging process allows for highly customizable designs, enabling engineers to create heat sinks tailored to the specific cooling requirements of their devices.
- What materials are commonly used in forged heat sinks?
Aluminum and copper are the most commonly used materials due to their excellent thermal conductivity and durability.
- Where can I find forged heat sinks for high-power devices?
Companies like PT Heat Sink offer a wide range of forged heat sinks designed for high-power applications. Their expertise ensures that you receive the best solution for your needs.