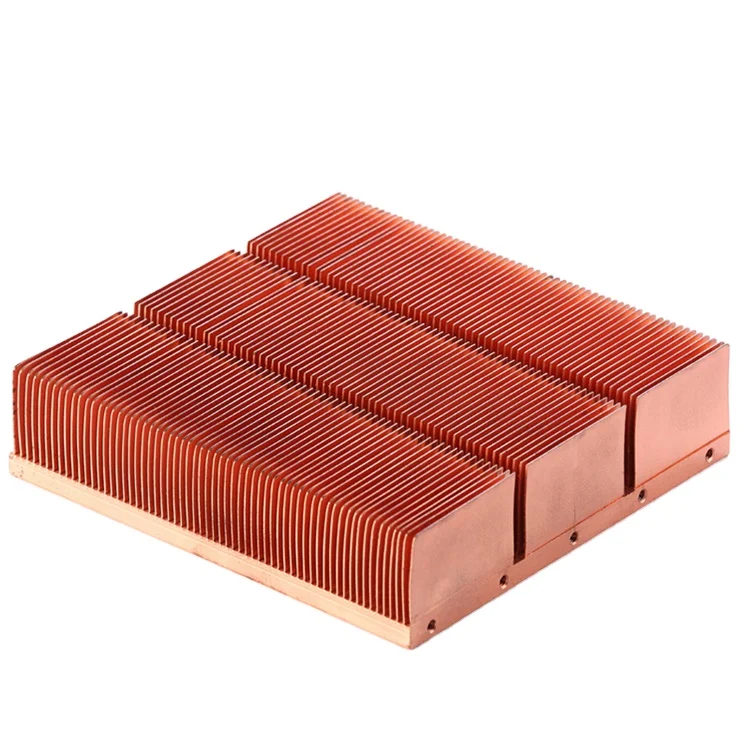
Efficient thermal management is critical to ensuring the reliability and longevity of electronic systems. As electronic devices become more powerful and compact, heat dissipation challenges grow, making the selection of appropriate heat sink materials and designs more crucial. The choice of heat sink materials not only affects performance but also plays a significant role in determining the cost-efficiency of a cooling solution. This article delves into the cost-benefit analysis of various heat sink materials and design methods, providing insights into their impact on thermal performance, weight, and application suitability.
Importance of Choosing the Right Heat Sink Materials and Designs
Selecting the right heat sink materials and design is key to achieving effective thermal management. Each material, whether it’s aluminum, copper, or advanced composites, has unique properties that influence heat dissipation, durability, and cost. Similarly, different design methods, such as pin fin and straight fin, affect how efficiently heat is transferred away from sensitive electronic components. In industries where heat management is vital for both safety and performance, understanding these nuances is essential for making informed decisions.
Overview of Heat Sink Materials
Heat sinks can be crafted from a variety of materials, with aluminum and copper being the most common. Each material comes with distinct thermal and mechanical properties that affect its efficiency and suitability for specific applications.
1. Aluminum
Aluminum is widely used for heat sinks due to its excellent balance between cost, thermal conductivity, and weight. With a thermal conductivity of around 205 W/mK, aluminum efficiently conducts heat away from electronic components while being relatively lightweight, making it ideal for portable devices. Aluminum heat sinks are also cost-effective, which explains their widespread use across industries.
Advantages:
- Lightweight, making it suitable for compact and portable electronics.
- Relatively affordable, providing cost-effective solutions for mass production.
- Adequate thermal conductivity for a wide range of applications.
Disadvantages:
- Less thermally conductive compared to copper, meaning it may not be ideal for high-performance applications requiring rapid heat dissipation.
2. Copper
Copper offers superior thermal conductivity compared to aluminum, with a value of 385 W/mK. This makes it an excellent choice for applications where efficient heat transfer is paramount, such as high-performance computing and industrial electronics. However, copper is heavier and more expensive than aluminum, which limits its use in certain applications where cost and weight are critical considerations.
Advantages:
- Superior thermal conductivity, making it ideal for performance-intensive applications.
- Excellent durability and reliability under extreme conditions.
Disadvantages:
- Heavier than aluminum, which can limit its use in portable devices.
- Higher cost, making it less suitable for cost-sensitive projects.
3. Advanced Composites
With the demand for lighter and more efficient cooling solutions, advanced composites have emerged as a new option for heat sink materials. These materials, which often combine elements like carbon fibers with metals or polymers, offer a unique blend of high thermal conductivity and reduced weight.
Advantages:
- Extremely lightweight, making them suitable for cutting-edge electronics where size and weight are critical.
- Can offer excellent thermal conductivity, especially in custom-designed applications.
Disadvantages:
- Expensive to produce, making them more suitable for niche applications.
- Limited availability and manufacturing complexity compared to aluminum or copper.
Heat Sink Design Techniques
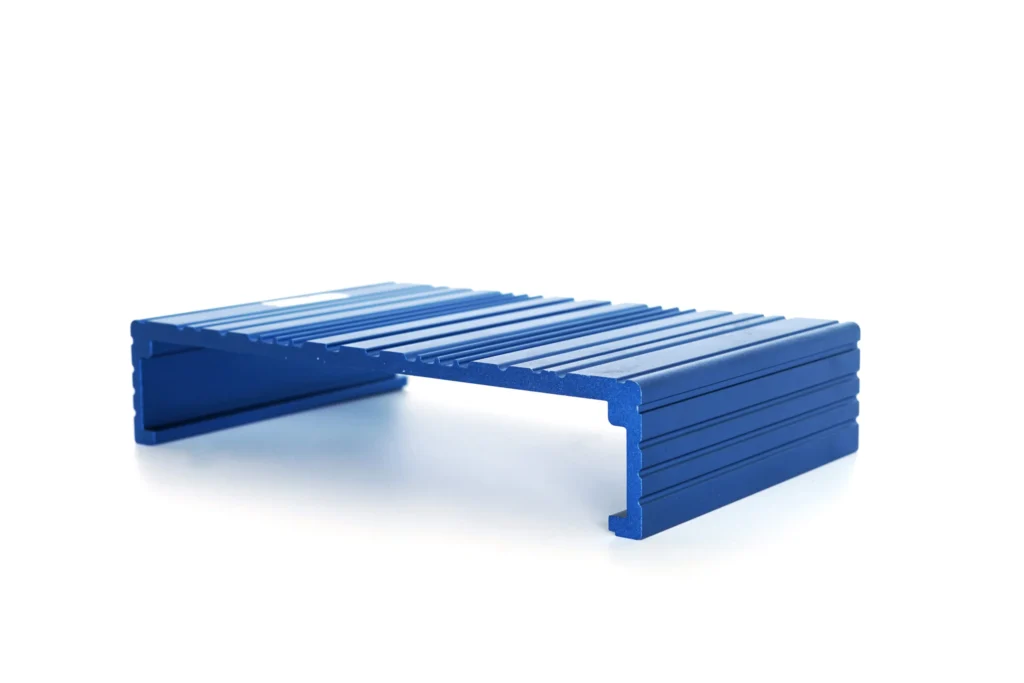
Apart from material selection, the design of a heat sink plays a significant role in its thermal performance. Common design techniques include pin fin, straight fin, and microchannel configurations, each offering distinct benefits in terms of heat dissipation.
1. Pin Fin Design
Pin fin heat sinks feature an array of vertically aligned pins that enhance airflow and maximize surface area. This design is highly effective for natural convection cooling, where airflow is passive. The large surface area allows for greater heat dissipation, making pin fin heat sinks an excellent choice for applications requiring minimal active cooling.
Advantages:
- Enhanced airflow and efficient heat dissipation through increased surface area.
- Suitable for both natural and forced convection cooling methods.
Disadvantages:
- Manufacturing complexity can increase costs, especially for custom designs.
2. Straight Fin Design
Straight fin heat sinks feature long, parallel fins that guide airflow across the surface. This design is typically used in forced convection cooling, where airflow is actively pushed through the fins using a fan. While not as efficient as pin fin designs for natural convection, straight fin heat sinks are cost-effective and easy to manufacture.
Advantages:
- Simple, cost-effective design with efficient heat dissipation in forced convection applications.
- Suitable for mass production due to ease of manufacturing.
Disadvantages:
- Limited performance in passive cooling applications, where airflow is restricted.
3. Microchannel Design
Microchannel heat sinks utilize a series of small channels to direct fluid or air across the surface for highly efficient cooling. These designs are often used in high-performance computing and aerospace applications, where precise temperature control is critical.
Advantages:
- Extremely high heat dissipation efficiency, especially in liquid cooling systems.
- Ideal for compact, high-power devices where space is limited.
Disadvantages:
- High manufacturing costs due to design complexity.
- Requires additional components, such as pumps for liquid cooling, which increase overall system cost.
Cost-Benefit Analysis of Heat Sink Materials
When conducting a cost-benefit analysis of heat sink materials, it’s crucial to balance the cost of the material against its thermal performance benefits. In many cases, aluminum offers the best overall balance between cost and efficiency, making it the go-to material for most consumer electronics. Copper, while more expensive, is indispensable for high-performance applications where heat dissipation needs to be maximized.
Aluminum vs. Copper
In typical consumer applications, the cost of aluminum heat sinks is often 30-40% lower than copper heat sinks. However, copper’s superior thermal conductivity means it may reduce the need for additional cooling components, such as fans, in high-power systems. This could offset its higher initial cost in certain scenarios.
Advanced Cooling Methods
As heat dissipation needs continue to grow, advanced cooling methods, such as phase change materials and liquid cooling, have gained popularity. These methods offer superior heat dissipation compared to traditional heat sinks but come with higher costs and complexity.
Phase Change Materials (PCM)
Phase change materials absorb heat by changing their state (from solid to liquid), making them effective in applications with periodic heat spikes. However, they are less efficient in continuous high-heat environments.
Advantages:
- Excellent at managing periodic heat spikes.
- Compact and lightweight.
Disadvantages:
- Limited use in continuous high-heat environments.
- Higher cost and complexity in manufacturing.
Liquid Cooling
Liquid cooling systems, often used in high-performance computers and industrial equipment, circulate coolant through channels to dissipate heat. These systems offer exceptional heat dissipation but require pumps, reservoirs, and other components, increasing both cost and maintenance requirements.
Advantages:
- Superior heat dissipation for high-performance applications.
- Suitable for systems requiring precise thermal control.
Disadvantages:
- Higher initial costs and maintenance requirements.
- Increased system complexity.
Future Trends in Heat Sink Design
As electronics continue to evolve, new materials and technologies are emerging that could revolutionize heat sink efficiency. Composite materials, such as graphene-infused heat sinks, offer the potential for even greater thermal conductivity at a fraction of the weight of traditional materials.
Moreover, computational modeling and artificial intelligence (AI) are becoming vital tools in optimizing heat sink designs. By simulating thermal conditions and adjusting designs in real-time, engineers can develop heat sinks that are tailored to specific applications, maximizing efficiency while minimizing costs.
Making the Right Choice for Your Needs
When selecting the appropriate heat sink material and design, it’s important to consider the specific operational requirements of your system. Aluminum remains the most versatile and cost-effective option for most applications, but copper and advanced composites are invaluable for high-performance systems. Additionally, design choices, such as pin fin or microchannel designs, can significantly affect heat dissipation efficiency.
For applications requiring innovative cooling methods, such as liquid cooling or phase change materials, the initial cost may be higher, but the long-term benefits in terms of system reliability and performance could justify the investment.
In the world of thermal management, selecting the right heat sink materials and designs is critical for optimizing performance and cost-efficiency. Aluminum and copper continue to dominate the market, each offering unique advantages in terms of thermal conductivity, weight, and cost.
As advanced materials and cooling techniques continue to evolve, the potential for more efficient heat sinks increases. By working with companies like PT Heat Sink, you can ensure that you choose the best solution for your needs—whether it’s a straightforward aluminum heat sink or a more sophisticated composite design.
FAQs
Q1. What is the best material for heat sinks?
Aluminum is the most commonly used heat sink material due to its balance between cost and thermal conductivity. Copper is better for high-performance applications but is more expensive.
Q2. How do heat sink designs affect cooling efficiency?
Different designs, such as pin fin and straight fin, impact how efficiently heat is dissipated. Pin fin designs are more effective for natural convection, while straight fin designs are suitable for forced convection.
Q3. What are advanced cooling methods, and are they worth the cost?
Advanced cooling methods, such as liquid cooling, offer superior heat dissipation but come with higher costs and complexity. They are typically used in high-performance applications.
Q4. How do I choose the right heat sink for my needs?
The choice of heat sink depends on your specific application, budget, and thermal requirements. For most consumer electronics, aluminum heat sinks are sufficient. However, for performance-driven systems, copper or advanced materials may be required.