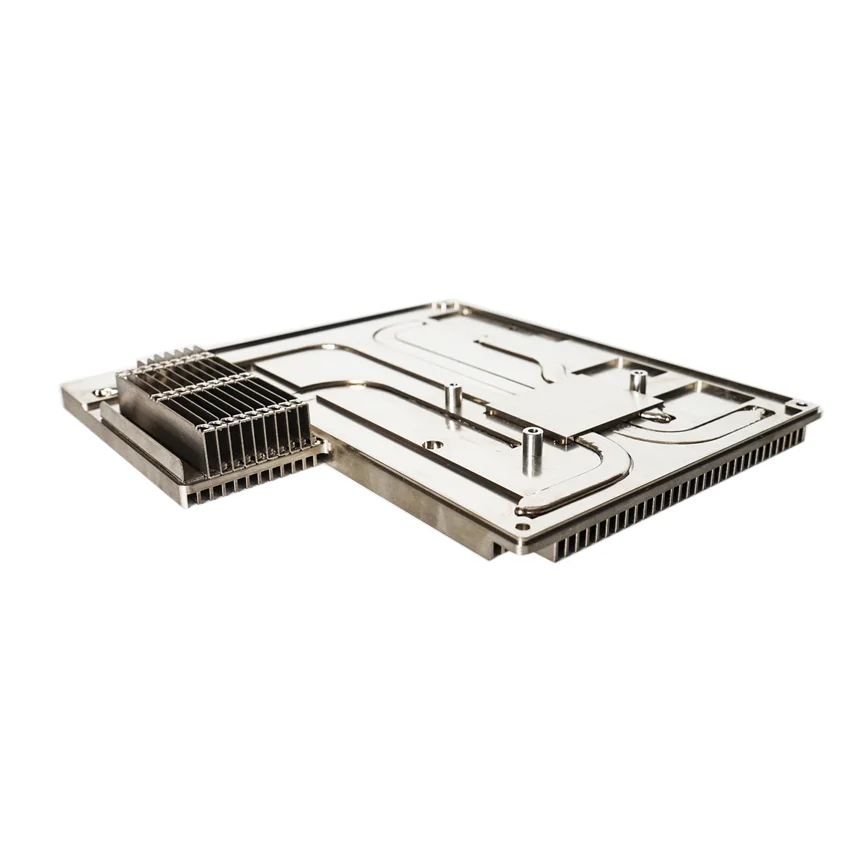
In today’s technology-driven industrial landscape, effective thermal management is more important than ever. Heat sinks play a crucial role in ensuring the reliability and performance of electronic components by dissipating excess heat and maintaining optimal operating temperatures. Whether it’s for high-powered machinery or compact electronics, choosing heat sinks tailored to your industrial application is key to avoiding overheating and ensuring long-term operational stability.
In this article, we’ll delve into the fundamentals of heat sink operation, explore various factors to consider when selecting one, and discuss how to optimize heat sink performance.
Understanding Heat Sink Fundamentals
Heat Sink Operation and Thermal Resistance
A heat sink’s primary function is to absorb and dissipate heat away from electronic components, preventing overheating and maintaining efficiency. The effectiveness of a heat sink is often measured in terms of thermal resistance, which refers to the heat sink’s ability to transfer heat from the component to the surrounding environment. Lower thermal resistance means the heat sink can dissipate heat more efficiently, ensuring the component stays cool even under high loads.
Thermal resistance depends on several factors, including the material used, the surface area of the heat sink, and the airflow around it. Proper heat sink selection requires a thorough understanding of the thermal requirements of the device and how much heat needs to be dissipated to maintain safe operating temperatures.
Types of Heat Sinks and Their Applications
There are several types of heat sinks, each suited to different industrial environments and applications. Understanding their differences can help you make an informed decision:
- Extruded Heat Sinks: These are the most common type, made by extruding metal (usually aluminum) through a die. They offer a good balance between cost, performance, and scalability, making them ideal for general-purpose applications.
- Stamped Heat Sinks: These are manufactured by stamping thin sheets of metal into the desired shape. They are typically more affordable and lightweight, making them suitable for lower power applications or where cost is a primary consideration.
- Forged Heat Sinks: These are created through a forging process, which results in a denser, stronger material. Forged heat sinks are often used in high-power applications where durability and performance are critical.
Each type has its strengths and limitations, which makes choosing heat sinks a nuanced process based on specific industrial requirements.
Factors to Consider When Choosing a Heat Sink
When it comes to selecting the right industrial heat sink, several factors need to be taken into account to ensure optimal performance. Here’s a detailed breakdown of the key considerations:
Power Dissipation Needs
The primary factor in heat sink selection is the amount of heat that needs to be dissipated. This is directly related to the power consumption of the device or system. Calculating the heat load accurately ensures that the selected heat sink will be able to handle the thermal demands of the application without overloading.
Ambient Temperature Conditions
The surrounding environment plays a significant role in determining the effectiveness of a heat sink. For example, a device operating in a cool, well-ventilated space may require a smaller heat sink compared to one in a hot or enclosed environment. High ambient temperatures reduce the ability of the heat sink to transfer heat, making it necessary to choose one with a lower thermal resistance or additional cooling mechanisms.
Spatial Constraints
Space limitations are another important factor in choosing heat sinks for industrial applications. Some industrial systems are compact, and the available space for a heat sink may be limited. In such cases, it is essential to select a heat sink design that maximizes surface area within a small footprint, such as a pin-fin or bonded-fin design, which allows for better airflow and heat dissipation in restricted spaces.
Importance of Thermal Resistance Calculation
Thermal resistance is a key metric in heat sink performance, and calculating it correctly is vital for heat sink selection. The total thermal resistance of a system is the sum of the thermal resistances of the heat sink, the thermal interface material (TIM), and the component itself. Ensuring that the heat sink’s thermal resistance is low enough to keep the component below its maximum operating temperature is essential for long-term reliability.
Material Selection
The material used in a heat sink greatly influences its thermal conductivity, weight, and overall performance. Let’s take a closer look at the most common materials and their respective properties.
Aluminum Heat Sinks
Aluminum is the most widely used material for heat sinks due to its excellent thermal conductivity, lightweight properties, and affordability. It’s also easy to manufacture into various shapes and sizes, making it suitable for a wide range of applications. However, aluminum may not be the best choice for high-power industrial applications where more efficient heat dissipation is required.
Copper Heat Sinks
Copper has superior thermal conductivity compared to aluminum, making it more efficient at transferring heat. This makes it a great choice for high-power applications where effective heat dissipation is critical. However, copper is heavier and more expensive than aluminum, which limits its use in applications where weight and cost are significant considerations.
Hybrid Heat Sinks
In some cases, hybrid designs that combine both copper and aluminum are used. These heat sinks feature a copper base to maximize heat transfer from the component and aluminum fins to dissipate the heat into the surrounding air. This design offers a balance between performance and cost, making it a popular choice for industrial applications requiring efficient cooling.
Design and Manufacturing Techniques
The design of a heat sink, including its shape, size, and manufacturing process, plays a crucial role in its ability to dissipate heat efficiently. Here’s an overview of common heat sink designs and manufacturing techniques.
Pin Fin vs. Straight Fin Designs
- Pin Fin Heat Sinks: Pin fin heat sinks are designed with numerous small pins that maximize surface area for heat dissipation. This design works well in applications with multi-directional airflow and limited space. Pin fin heat sinks are particularly effective in natural convection environments.
- Straight Fin Heat Sinks: Straight fin designs feature parallel fins that provide an increased surface area for heat transfer. These heat sinks are more suitable for forced convection environments, where airflow is directed along the length of the fins. Straight fin heat sinks are commonly used in systems with active cooling solutions like fans or blowers.
Manufacturing Processes: Skiving, Die-Casting, and CNC Machining
- Skiving: Skiving is a process that involves slicing thin fins from a block of metal to create a heat sink. This method results in high-performance heat sinks with excellent thermal properties, as there are no gaps between the fins and the base. Skived heat sinks are ideal for applications requiring precise thermal management.
- Die-Casting: Die-casting involves pouring molten metal into a mold to create the heat sink. While this process is cost-effective for high-volume production, it may result in lower thermal performance compared to other methods due to the presence of air gaps or imperfections in the casting.
- CNC Machining: CNC machining is a highly precise method used to create custom heat sink designs with tight tolerances. It offers flexibility in producing complex shapes but can be more expensive than other manufacturing processes.
Advanced Cooling Solutions
In some industrial applications, traditional heat sinks may not provide sufficient cooling, and more advanced solutions are required.
Liquid Cooling Systems
Liquid cooling systems use a fluid to transfer heat away from components. These systems are highly efficient and are often used in high-power applications where air cooling alone is insufficient. Liquid cooling systems can handle higher heat loads and provide more consistent cooling, making them ideal for data centers, industrial automation, and high-performance computing.
Thermoelectric Coolers
Thermoelectric coolers (TECs) use the Peltier effect to create a temperature difference between two sides of a thermoelectric module. These coolers are highly precise and can maintain stable temperatures, even in fluctuating ambient conditions. TECs are often used in sensitive electronic applications, such as medical devices and scientific instruments, where maintaining precise temperature control is critical.
Optimizing Heat Sink Performance
Optimizing heat sink performance requires careful consideration of several factors, including design, material selection, and thermal interface materials (TIMs).
Fin Design and Airflow Optimization
The fin design of a heat sink plays a significant role in its ability to dissipate heat. Increasing the number of fins or optimizing their shape can enhance heat dissipation by increasing surface area and improving airflow. Fin designs like serrated or slotted fins can further improve airflow dynamics, particularly in forced convection systems.
Thermal Interface Materials (TIMs)
Using high-quality thermal interface materials (TIMs) is essential for improving the heat transfer between the component and the heat sink. TIMs fill microscopic gaps between the surfaces, allowing for more efficient heat conduction. Common TIMs include thermal paste, pads, and phase-change materials, each offering varying levels of performance based on the application.
Selecting the right industrial heat sink is essential for maintaining the reliability and performance of your electronics. By considering factors such as power dissipation, ambient temperature, material properties, and design, you can choose a heat sink that meets your specific needs. Whether you’re working with traditional air cooling or exploring advanced solutions like liquid cooling, partnering with experts like PT Heat Sink can help you find the perfect thermal management solution for your application.
FAQs
1. What factors should I consider when choosing a heat sink?
Key factors include power dissipation needs, ambient temperature conditions, spatial constraints, and thermal resistance. The material of the heat sink and its design (such as fin structure) also play a crucial role in optimizing performance.
2. How do I calculate thermal resistance for heat sink selection?
Thermal resistance is calculated by dividing the temperature difference between the heat source and the ambient environment by the heat dissipation (power) in watts. Lower thermal resistance ensures better heat dissipation, helping you select a heat sink with adequate performance.
3. What is the difference between aluminum and copper heat sinks?
Aluminum is lighter and more affordable, making it ideal for general applications. Copper offers superior thermal conductivity, making it a better choice for high-power applications where efficient heat dissipation is crucial, though it is heavier and more expensive.
4. When should I consider advanced cooling solutions like liquid cooling?
Advanced cooling solutions like liquid cooling are necessary when traditional air cooling methods are insufficient to manage the heat load. This typically occurs in high-performance applications such as data centers, automotive systems, or industrial machinery with high thermal output.