Heat is a natural byproduct of electronics, from the smallest smartphone to the largest industrial machines. Managing this heat is crucial to ensure that these devices function correctly and safely. That’s where heat sinks come in. A heat sink is a component that helps dissipate heat, keeping everything running smoothly. Whether you’re working with a computer server, an electric vehicle, or even medical equipment, choosing the right heat sink for your application is key to maintaining performance and reliability.
Key Factors in Choosing the Right Heat Sink
Understanding Thermal Requirements
Before choosing a heat sink, you need to understand your device’s thermal requirements. Every electronic device generates heat when it operates, and the amount of heat varies based on its power output. High-power devices generate more heat, which needs to be managed efficiently to prevent overheating. It’s essential to know how much heat your device produces and the environmental conditions it will operate in. For example, a device used in a hot, humid environment will need a more robust cooling solution than one used in a climate-controlled space.
Material Selection
The material of the heat sink is critical to its performance. The most common materials are aluminum and copper. Aluminum is lightweight, affordable, and has good thermal conductivity, making it ideal for many applications. Copper, on the other hand, has even better thermal conductivity but is heavier and more expensive. Sometimes, a combination of both materials is used to balance performance and cost. When selecting a material, it’s important to consider not only its thermal properties but also its weight and cost, especially if you’re working with weight-sensitive applications like automotive or aerospace.
Heat Sink Design and Configuration
The design and configuration of the heat sink significantly impact its performance. Different fin designs, such as straight fins, pin fins, or skived fins, influence how air moves through the heat sink and how effectively heat is dissipated. In some cases, integrating heat pipes or vapor chambers into the design can enhance thermal performance, especially in high-power applications. Custom designs tailored to specific applications often outperform standard, off-the-shelf heat sinks.
Detailed Analysis of Heat Sink Types
Extruded Heat Sinks
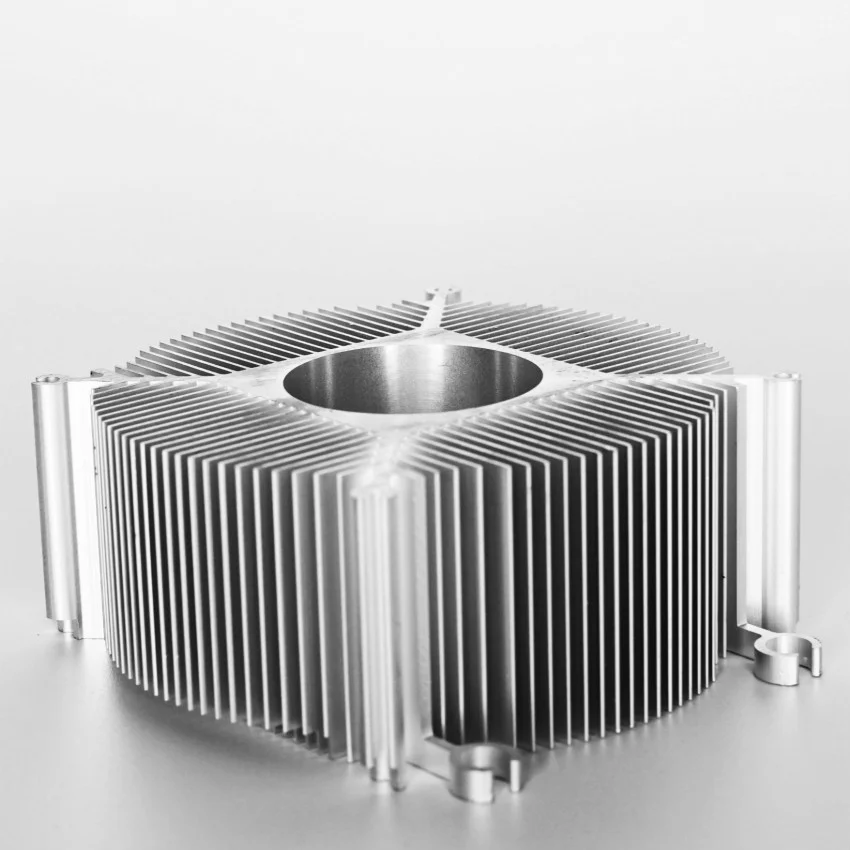
Extruded heat sinks are among the most commonly used types due to their cost-effectiveness and versatility. They are manufactured by pushing aluminum through a die, forming it into the desired shape. This process allows for a variety of complex shapes, making it possible to optimize the heat sink for different applications. Extruded heat sinks are lightweight and can be finished in various ways, such as anodizing, which improves corrosion resistance and heat dissipation.
Heat Pipe Heat Sinks

Heat pipe heat sinks use a combination of heat pipes and fins to transfer and dissipate heat. Heat pipes are sealed tubes filled with a liquid that vaporizes and moves heat from one end of the pipe to the other. This method is highly efficient, making heat pipe heat sinks ideal for high-power applications where traditional air-cooled heat sinks may not suffice. They are commonly used in servers, telecommunications equipment, and high-performance computers.
Die-Cast Heat Sinks
Die-cast heat sinks are made by injecting molten metal into a mold, allowing for high-speed production and complex shapes. This process is ideal for mass production, making die-cast heat sinks a cost-effective solution for large-scale applications. Die-casting can be used to create intricate designs that are not possible with extrusion or other methods, allowing for more efficient cooling in compact spaces.
Cold Forged Heat Sinks
Cold forged heat sinks are manufactured by compressing metal into shape under high pressure, without heating the material. This process produces heat sinks with high thermal conductivity and strength. Cold forging is especially suitable for creating pin fin designs, which are effective in applications where weight is a concern, such as in aerospace and automotive industries.
Skived Fin Heat Sinks
Skived fin heat sinks are made by cutting fins from a solid block of metal, creating a high fin density and surface area. This manufacturing process allows for precise control over fin thickness and spacing, resulting in heat sinks with superior thermal performance. Skived fin heat sinks are ideal for applications that require maximum heat dissipation in a compact space.
Liquid Cooling Plates
Liquid cooling plates are used in applications where air cooling is insufficient. These plates typically consist of channels through which a liquid coolant flows, absorbing heat from the surrounding components. Liquid cooling is highly effective in managing high heat fluxes and is commonly used in power electronics, automotive applications, and high-performance computing.
Vapor Chambers
Vapor chambers are flat, sealed chambers that contain a small amount of liquid. As heat is applied to one area, the liquid evaporates, and the vapor spreads across the chamber, evenly distributing the heat. Vapor chambers are highly efficient and are often used in applications where space is limited, and high heat transfer is required, such as in smartphones, laptops, and other compact electronics.
Industry-Specific Heat Sink Applications
Storage Energy and Solar Inverters
In the energy storage and solar inverter industries, reliable thermal management is crucial. Heat sinks help manage the heat generated by power conversion and storage devices, ensuring that they operate efficiently and have a long lifespan. Custom heat sinks designed for these applications can improve energy efficiency and reduce maintenance costs.
Automotive Applications
The automotive industry increasingly relies on advanced thermal management solutions, particularly in electric vehicles (EVs). Heat sinks in EVs manage the heat generated by batteries, power electronics, and motors, ensuring that these components operate within safe temperature ranges. Lightweight, high-performance heat sinks are essential to maintain vehicle efficiency and performance.
Data Centers and AI
Data centers and AI systems generate significant amounts of heat due to the high density of computing equipment. Effective thermal management is critical to prevent overheating and ensure continuous operation. Advanced cooling solutions, such as heat pipe heat sinks and liquid cooling plates, are often required to handle the heat load in these environments.
Telecommunications and Medical Equipment
In telecommunications and medical equipment, compact and efficient heat sinks are necessary to maintain the performance and reliability of sensitive electronics. These industries often require custom-designed heat sinks that can meet strict size and performance criteria while ensuring reliable operation in various environments.
Designing Custom Heat Sinks
Collaboration with Experts
Designing a custom heat sink requires collaboration with experienced engineers who understand the specific thermal needs of your application. At PTHeatsink, our team of engineers has over 20 years of experience in thermal management. We use advanced simulation tools, such as CFD (Computational Fluid Dynamics), SolidWorks, ProE, and AutoCAD, to design heat sinks that meet your exact specifications.
Prototyping and Testing
Prototyping is a critical step in the heat sink design process. It allows for testing and validation of the design before full-scale production. At PTHeatsink, we create prototypes using the same materials and manufacturing processes that will be used in the final product, ensuring that the prototype accurately represents the finished heat sink. Rigorous testing ensures that the heat sink meets all performance and reliability requirements.
Cost Considerations
While performance is paramount, cost is also a critical factor in heat sink design. At PTHeatsink, we work closely with our clients to balance performance with budget considerations. Our 91,000 square foot facility allows us to offer competitive pricing, especially for high-volume production runs. By optimizing the design and manufacturing process, we can deliver high-performance heat sinks at a cost that fits within your budget.
Why Choose PTHeatsink for Your Heat Sink Needs
Expertise and Experience
With over 20 years of experience in the heat sink industry, PTHeatsink is a trusted partner for companies around the world. We have completed over 3,000 designs, providing reliable and efficient thermal solutions to industries ranging from automotive to telecommunications. Our clients include some of the world’s leading brands, such as LG, HP, and Stellantis.
Advanced Manufacturing Capabilities
PTHeatsink’s 91,000 square foot facility is equipped with the latest manufacturing technologies, including CNC machining, extrusion, stamping, cold forging, die casting, skiving, and heat pipe assembly. Our advanced capabilities allow us to produce heat sinks that meet the highest quality standards while offering competitive pricing.
Customer Support and Service
At PTHeatsink, we pride ourselves on providing exceptional customer support. Our professional sales team ensures seamless communication throughout the design and production process. From initial consultation to final delivery, we are committed to meeting your thermal management needs with high-quality, cost-effective solutions.
Choosing the right heat sink is critical to ensuring the reliability and performance of your electronic devices. By understanding your thermal requirements, selecting the right materials, and working with experienced professionals, you can design a heat sink that meets your specific needs. At PTHeatsink, we offer a comprehensive range of custom heat sinks, backed by decades of expertise and advanced manufacturing capabilities. Contact us today to learn how we can help you with your thermal management needs.