Aluminum heat sinks are pivotal in managing the heat dissipation for a range of electronic devices, from CPUs and GPUs to LED lights and power transistors. Their role in extending the lifespan and enhancing the performance of electronic components cannot be overstated. This article explores the aluminum heat sink manufacturing process, detailing the steps involved and the significance of each stage in ensuring optimal thermal management solutions.
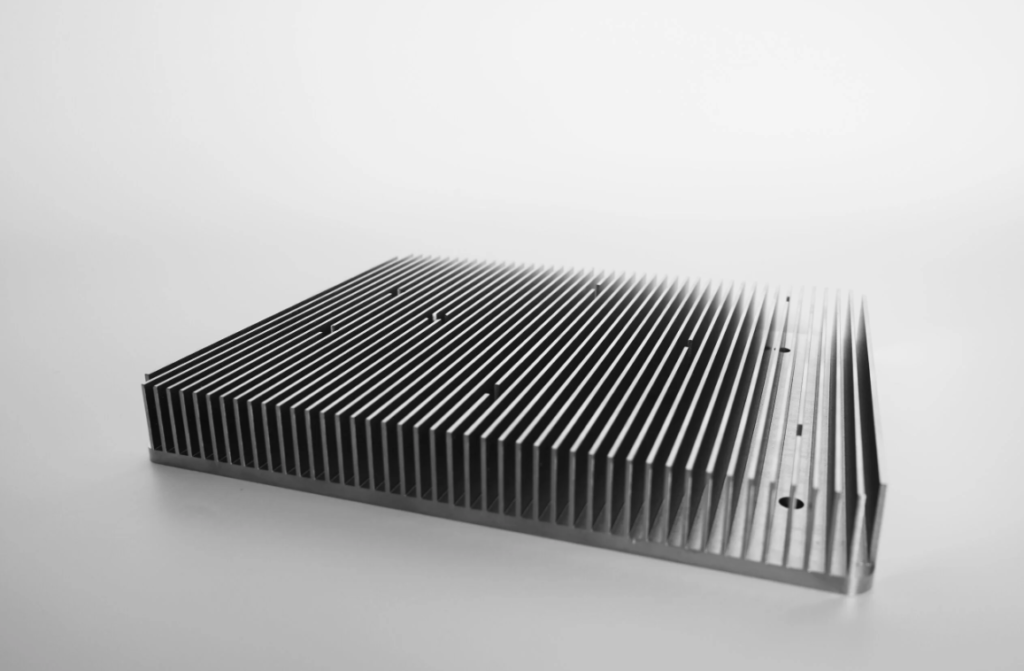
Understanding Aluminum Heat Sinks
Aluminum is the material of choice for heat sinks due to its excellent thermal conductivity and lightweight properties. It is also highly workable, which allows for the creation of complex geometries necessary to increase the surface area that dissipates heat. The process of manufacturing aluminum heat sinks involves several precise and technologically advanced techniques that contribute to the effectiveness of the final product.
Key Stages in Aluminum Heat Sink Manufacturing
1. Design and Engineering
The journey of creating an effective aluminum heat sink begins with a meticulous design process. Utilizing advanced software, engineers design the heat sink to maximize its surface area, which is crucial for effective heat dissipation. During this phase, considerations about the fin arrangement, thickness, and overall dimensions are meticulously planned to meet specific cooling requirements.
2. Material Selection
Choosing the right grade of aluminum is critical. The most commonly used aluminum alloys for heat sinks include 6061 and 6063, known for their excellent thermal conductivity and machinability. The choice depends on the required thermal performance and the manufacturing method being employed.
3. Manufacturing Processes
There are several methods used to manufacture aluminum heat sinks, each suitable for different applications and complexity levels:
a. Extrusion
The extrusion process involves forcing molten aluminum through a pre-designed die to create shapes that are optimal for heat dissipation. This method is cost-effective and suitable for producing heat sinks with straight, parallel fins, ideal for standard electronic devices.
b. Die Casting
Die casting is used for complex heat sink designs. It involves injecting molten aluminum under high pressure into a steel mold. This method is excellent for mass production and allows for the integration of features such as mounting points and complex fin structures.
c. CNC Machining
For prototypes or low-volume production, CNC machining is often employed. This method provides exceptional precision and allows for the creation of intricate and detailed designs that are not possible with extrusion or die casting.
d. Skiving
Skiving involves slicing thin layers of aluminum from a block to form fins. This method allows for very tight fin spacing and high fin density, which can significantly improve the heat sink’s performance.
4. Surface Treatment
After the heat sinks are manufactured, they undergo various surface treatments to enhance their thermal efficiency and corrosion resistance. These treatments include anodizing, which enhances the emissivity of the heat sink, and powder coating, which can be used for aesthetic purposes or to provide additional environmental protection.
5. Quality Assurance and Testing
The final stage in the manufacturing process is quality assurance and testing. Each batch of heat sinks is rigorously tested to ensure they meet the thermal performance standards required. This may involve thermal resistance testing, pressure drop testing, and longevity testing.
Applications of Aluminum Heat Sinks
Aluminum heat sinks are utilized in a broad spectrum of industries due to their efficient heat dissipation properties. In the electronics industry, they are crucial for preventing overheating in devices like laptops and smartphones. In lighting, aluminum heat sinks are essential components in LED lighting systems to prevent overheating and extend the life of the lights. The automotive industry also relies on aluminum heat sinks in various applications, including in electric vehicle battery management systems and LED headlights.a
The manufacturing process of aluminum heat sinks is a detailed and highly technical procedure that plays a critical role in the performance of many electronic systems. By understanding the complexities involved in each step from design to testing, manufacturers can create highly effective heat sinks that meet the specific cooling needs of modern electronics. As technology advances, the demand for efficient and precise aluminum heat sink manufacturing will continue to grow, making it a crucial element in the thermal management industry.
For those interested in integrating superior cooling solutions into their electronic products, exploring the advancements in aluminum heat sink technology is essential. Visit Ptheatsink.com to discover a range of innovative aluminum heat sink solutions designed to enhance device performance and durability.