In today’s fast-paced technological world, efficient cooling solutions are critical to the performance and longevity of electronic devices. As devices become more powerful and compact, the challenge of managing heat effectively has never been greater. This article dives into the world of cold forged pin fin heat sinks, exploring how they can revolutionize electronic cooling solutions across various industries.
As we continue to push the boundaries of technology, electronic devices are becoming more powerful, resulting in increased heat generation. Without effective cooling, these devices are at risk of overheating, leading to reduced performance, potential damage, and a shorter lifespan. From data centers and telecommunications to automotive and medical equipment, efficient thermal management is crucial for maintaining optimal performance and reliability.
Cold forged pin fin heat sinks are emerging as a leading solution for thermal management in high-performance electronics. Unlike traditional heat sinks, which may be extruded, die-cast, or machined, cold forged pin fin heat sinks are manufactured using a process that enhances their thermal properties and durability. This article will explore the benefits of these innovative heat sinks and how they can be applied to improve electronic cooling across various industries.
This article aims to provide an in-depth understanding of cold forged pin fin heat sinks, highlighting their unique advantages and the ways they can enhance cooling solutions for electronic devices. We will also explore how PTHeatsink, a leading manufacturer in the industry, leverages this technology to provide high-quality, cost-effective thermal solutions.
Understanding Cold Forging Technology
Cold forging is a manufacturing process that involves shaping metal under high pressure at room temperature. Unlike hot forging, which is performed at high temperatures, cold forging preserves the metal’s crystalline structure, resulting in a stronger, more durable product. This process is particularly advantageous for creating components that require high strength and precision, such as heat sinks.
In the context of heat sink manufacturing, cold forging allows for the creation of complex geometries, such as pin fin designs, with exceptional accuracy. The process also enables the use of materials with high thermal conductivity, such as aluminum and copper, ensuring that the heat sinks efficiently transfer heat away from electronic components.
Advantages of Cold Forging for Heat Sinks
Cold forging offers several benefits over other manufacturing methods, particularly in the context of heat sink production:
- Superior Material Properties: Cold forged heat sinks have enhanced mechanical strength, making them more resistant to deformation and wear.
- High Thermal Conductivity: The cold forging process maintains the high thermal conductivity of the base material, ensuring efficient heat dissipation.
- Cost-Effective Production: Cold forging is well-suited for mass production, offering a cost-effective solution for large-scale manufacturing.
- Precision and Consistency: Cold forging allows for the production of heat sinks with consistent quality and precise geometries, essential for effective thermal management.
The Role of Cold Forging in Heat Sink Design
Cold forging is instrumental in creating pin fin heat sinks, which are designed to maximize surface area and enhance heat dissipation. The process allows for the precise formation of pin fins, which are small, cylindrical projections that extend from the base of the heat sink. These fins increase the surface area available for heat transfer, improving the heat sink’s overall efficiency.
The Science Behind Pin Fin Heat Sink Design
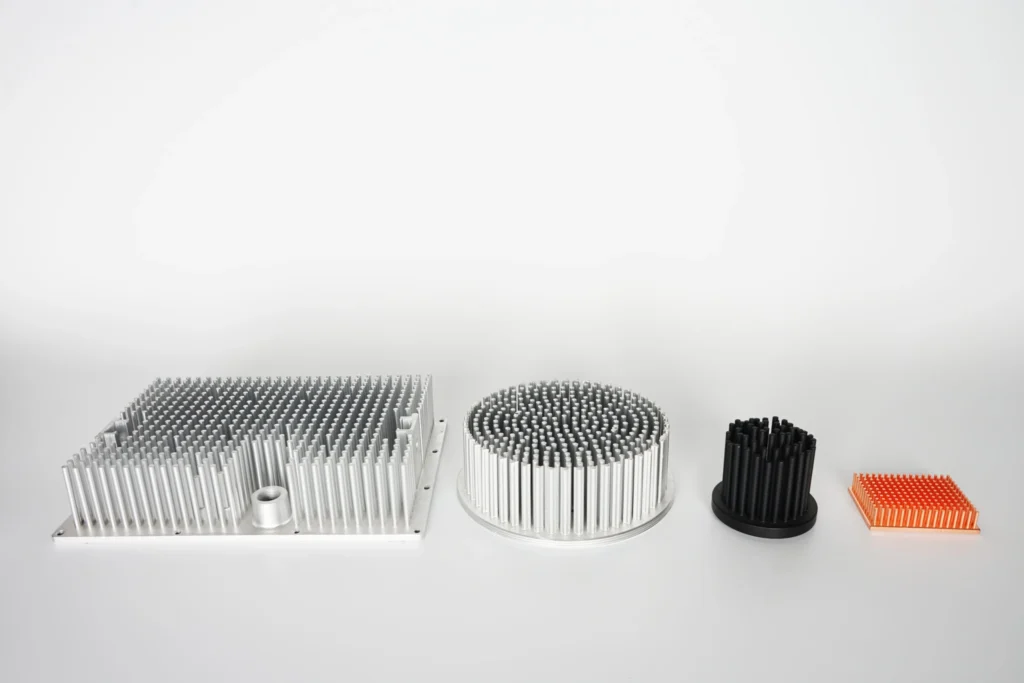
How Pin Fin Geometry Enhances Heat Dissipation
The design of pin fin heat sinks is rooted in the principles of thermodynamics. By increasing the surface area of the heat sink, pin fins allow for more efficient heat transfer from the electronic component to the surrounding air. The cylindrical shape of the fins also promotes airflow, reducing thermal resistance and improving cooling performance.
Pin fin heat sinks are particularly effective in applications where space is limited, and high-performance cooling is required. The fins create turbulence in the airflow, which enhances heat transfer by disrupting the boundary layer of air that forms around the heat sink. This design feature makes pin fin heat sinks ideal for use in high-power electronics, where managing heat is critical to maintaining performance and reliability.
Benefits of Pin Fin Design in Different Applications
Pin fin heat sinks offer several advantages in a variety of applications:
- Natural and Forced Convection: Pin fin heat sinks perform well in both natural and forced convection environments. In natural convection, the fins enhance heat dissipation by increasing surface area, while in forced convection, they create turbulence that improves heat transfer.
- Versatility: The pin fin design is versatile and can be customized to meet the specific cooling requirements of different industries, from telecommunications to automotive electronics.
- Space Efficiency: Pin fin heat sinks are compact and can be used in applications where space is limited, making them ideal for modern electronic devices that require efficient cooling in a small form factor.
Comparison with Other Heat Sink Designs
When compared to other heat sink designs, such as straight fin or skived fin heat sinks, pin fin heat sinks offer distinct advantages:
- Better Performance in Confined Spaces: Pin fin heat sinks are more effective in applications where space is limited, as their compact design allows for efficient cooling in tight spaces.
- Improved Airflow: The cylindrical shape of the pin fins promotes airflow and reduces thermal resistance, making them more effective in high-performance applications.
- Customization: Pin fin heat sinks can be customized to meet specific cooling requirements, offering greater flexibility than other designs.
Cold Forged Pin Fin Heat Sinks in Electronic Cooling
Enhanced Cooling Efficiency
Cold forged pin fin heat sinks are designed to maximize cooling efficiency by enhancing heat dissipation and reducing thermal resistance. The cold forging process allows for the precise formation of pin fins, which increases the surface area of the heat sink and improves airflow. This results in more efficient heat transfer from the electronic component to the surrounding air, keeping devices cool and preventing overheating.
Application-Specific Benefits
Cold forged pin fin heat sinks offer specific benefits across various industries:
- Telecommunications: In telecommunications, where devices operate at high frequencies, managing heat is critical to maintaining signal integrity and preventing equipment failure. Cold forged pin fin heat sinks provide efficient cooling for high-frequency devices, ensuring reliable performance.
- Data Centers: In data centers, where servers generate significant heat, cold forged pin fin heat sinks help maintain optimal operating temperatures, improving performance and reducing the risk of overheating.
- Automotive: In the automotive industry, where electronic components are exposed to harsh environments, cold forged pin fin heat sinks offer reliable cooling solutions that can withstand extreme temperatures and vibrations.
- Medical Equipment: In medical equipment, where precision and reliability are paramount, cold forged pin fin heat sinks ensure that devices operate within safe temperature ranges, preventing malfunctions and ensuring patient safety.
- Artificial Intelligence: AI processors generate substantial amounts of heat during operation. Cold forged pin fin heat sinks are essential in managing this heat, ensuring that AI systems run efficiently and reliably.
Long-Term Durability and Reliability
Cold forged pin fin heat sinks are known for their durability and reliability. The cold forging process results in a heat sink that is resistant to thermal cycling and mechanical stress, ensuring long-term performance even in demanding environments. This makes them ideal for applications where reliability is critical, such as in automotive electronics and medical equipment.
PTHeatsink’s Expertise in Cold Forged Pin Fin Heat Sinks
PTHeatsink, established in 2003 in Dongguan, China, is a leading provider of high-quality, cost-effective thermal solutions. With a 91,000 square foot facility and branch offices in the United States and Singapore, PTHeatsink specializes in the research, design, and manufacturing of custom heat sinks, including cold forged pin fin designs.
Specialized Manufacturing Processes
PTHeatsink utilizes state-of-the-art manufacturing processes to produce cold forged pin fin heat sinks that meet the highest standards of quality and performance:
- Custom Design and Prototyping: PTHeatsink’s team of seasoned engineers works closely with customers to design heat sinks tailored to their specific needs. Using advanced software such as CFD, Solidworks, and AutoCAD, PTHeatsink can create prototypes that meet precise thermal and mechanical requirements.
- State-of-the-Art Production: PTHeatsink’s manufacturing facility is equipped with advanced cold forging equipment, allowing for the production of high-quality pin fin heat sinks at scale.
- Quality Assurance: Every heat sink produced by PTHeatsink undergoes rigorous testing and quality assurance processes. The company is ISO9001, ISO14001, and IATF16949 certified, and its products are compliant with RoHS and REACH standards.
Competitive Advantages
PTHeatsink offers several competitive advantages:
- Cost-Effectiveness: PTHeatsink’s large-scale production capabilities allow the company to offer high-quality heat sinks at competitive prices.
- Experience and Expertise: With over 20 years of experience in the heat sink industry, PTHeatsink’s team of engineers has successfully completed over 3,000 designs.
- Premium Support: PTHeatsink’s professional sales team provides seamless communication and support, ensuring that customers receive the best possible service.
Industry Applications of Cold Forged Pin Fin Heat Sinks
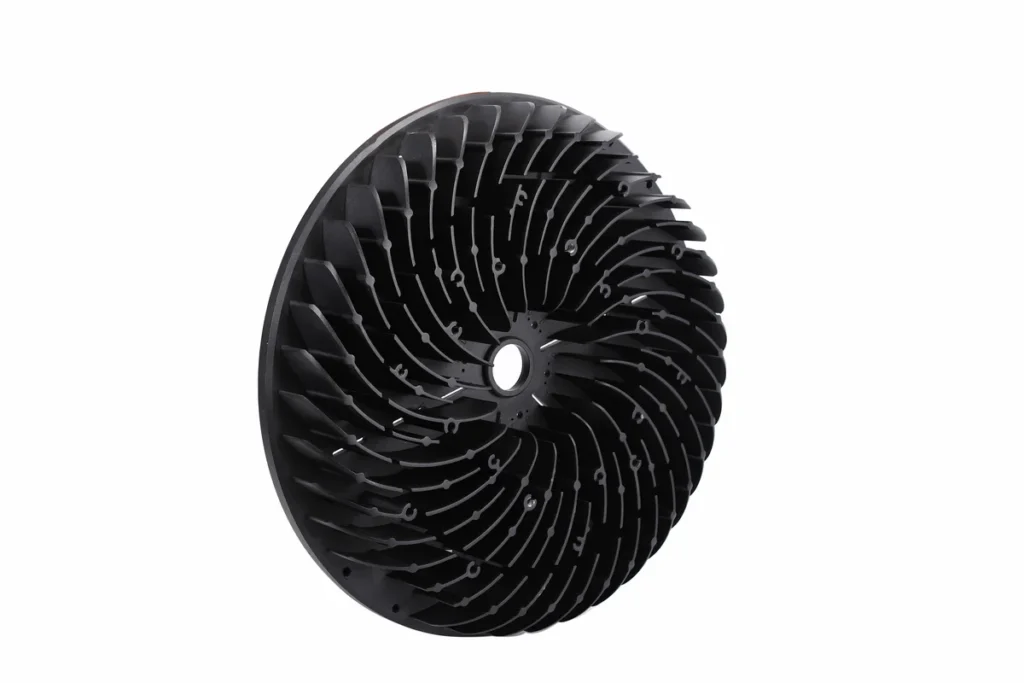
Specific Industry Use Cases
Cold forged pin fin heat sinks are used in a variety of industries, each with its unique cooling challenges:
- Energy Storage Systems: In energy storage systems, such as those used in solar inverters, managing heat is critical to maintaining efficiency and extending the lifespan of the system. Cold forged pin fin heat sinks provide effective cooling, ensuring that the system operates at peak performance.
- Computer Servers: In computer servers, where high-performance processors generate significant heat, cold forged pin fin heat sinks help maintain optimal operating temperatures, improving performance and preventing downtime.
- Renewable Energy: In renewable energy applications, such as wind turbines, cold forged pin fin heat sinks provide reliable cooling solutions that can withstand the harsh environmental conditions often associated with these systems.
Future Trends in Heat Sink Technology
As technology continues to evolve, the demand for efficient cooling solutions will only increase. Emerging trends such as the miniaturization of electronic components, the rise of AI and IoT, and the push for higher power densities will drive innovation in heat sink technology. Cold forged pin fin heat sinks, with their superior thermal performance and versatility, are well-positioned to meet these challenges.
Cold forged pin fin heat sinks represent a significant advancement in thermal management technology, offering superior cooling performance, durability, and versatility. Whether used in telecommunications, data centers, automotive electronics, or medical equipment, these heat sinks provide reliable and efficient cooling solutions that enhance the performance and longevity of electronic devices.
If you’re looking for high-quality, cost-effective thermal solutions, consider PTHeatsink’s cold forged pin fin heat sinks. With over 20 years of experience and a commitment to excellence, PTHeatsink is well-equipped to meet your thermal management needs. Contact PTHeatsink today to learn more about how they can help you with your next project.
As the demand for efficient cooling solutions continues to grow, cold forged pin fin heat sinks will play an increasingly important role in ensuring that electronic devices operate at their best. With ongoing innovations in heat sink technology and a focus on quality and performance, PTHeatsink is poised to lead the way in the next generation of thermal management solutions.
Frequently Asked Questions (FAQ)
1. What is a cold forged pin fin heat sink?
A cold forged pin fin heat sink is a type of heat sink manufactured using a cold forging process that enhances its thermal properties and durability. It features small, cylindrical fins that increase surface area and improve heat dissipation.
2. How does cold forging improve the performance of heat sinks?
Cold forging maintains the high thermal conductivity of the base material and allows for the precise formation of complex geometries, resulting in heat sinks that are both strong and efficient at dissipating heat.
3. What are the advantages of pin fin heat sinks over other types?
Pin fin heat sinks offer superior cooling performance in confined spaces, improved airflow, and the ability to be customized for specific applications.
4. In which industries are cold forged pin fin heat sinks most commonly used?
They are commonly used in telecommunications, automotive, data centers, medical equipment, and energy storage systems.
5. How does the geometry of pin fins enhance heat dissipation?
The pin fin design increases surface area and promotes airflow, which reduces thermal resistance and improves heat dissipation.
6. What materials are typically used in cold forged pin fin heat sinks?
Aluminum and copper are the most commonly used materials due to their high thermal conductivity.
7. What makes PTHeatsink a leading manufacturer of cold forged pin fin heat sinks?
PTHeatsink combines over 20 years of industry experience with advanced manufacturing techniques, ensuring high-quality, cost-effective thermal solutions for a wide range of industries.
8. How does PTHeatsink ensure the quality and reliability of its products?
PTHeatsink implements rigorous testing and quality assurance processes, including ISO9001, ISO14001, and IATF16949 certifications, to ensure that every product meets the highest standards.
9. What are the steps involved in PTHeatsink’s custom heat sink design process?
PTHeatsink’s design process involves close collaboration with customers, using advanced software to create prototypes that meet precise thermal and mechanical requirements before moving into full-scale production.
10. How can I get a quote or consultation for a custom heat sink project with PTHeatsink?
You can contact PTHeatsink through their website or by phone to request a quote or consultation. The company’s sales team is available 24/7 to assist with your inquiries.